www.konstruktion-industrie.com
18
'17
Written on Modified on
Ein praxisorientierter Ansatz zur Vermeidung von ineffizientem Ressourceneinsatz in der Fertigung
Hersteller suchen stets nach Wegen, um Produktivität und Effizienz zu maximieren. Heutzutage gehen diese Bemühungen häufig mit komplexen Programmen einher, bei denen Schlagwörter wie Cloud Computing, datengestützte Fertigung, cyberphysische Systeme und Industry4.0 fallen. Die Konzepte hinter diesen innovativen Programmen sind bemerkenswert und es lassen sich damit beeindruckende Ergebnisse erzielen. Häufig lassen sich die ambitionierten Pläne jedoch nicht mit der Fertigungspraxis in Einklang bringen, wobei unkontrollierte Verschwendung im Fertigungsprozess ein kritisches Faktum ist. Bevor ein Hersteller über Digitalisierung und Optimierung nachdenkt, muss er zunächst seine Prozesse untersuchen und ermitteln, wo Verschwendung auftritt, um dann Methoden zu entwickeln, wie sie reduziert oder vermieden werden kann. Verschwendungskontrolle ist der erste Schritt, um einen Fertigungsbetrieb auf die Einführung komplexer intelligenter Fertigungsstrategien vorzubereiten. Abbildung 1 – Gesamtbild aller Elemente in einem Fertigungsbetrieb und ihrer Beziehungen und Interaktionen untereinander (Modell und Konzept: NEXT STEP).
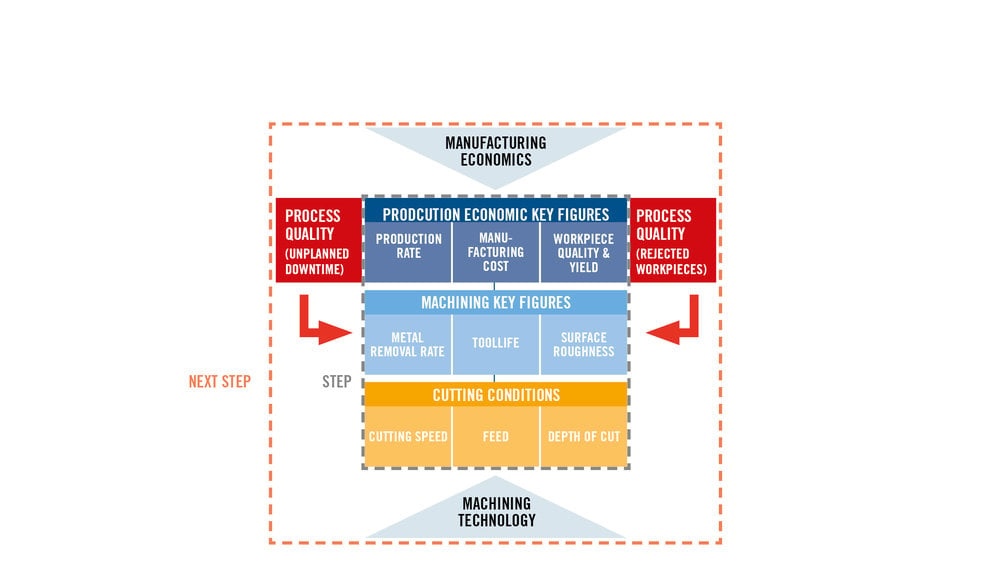
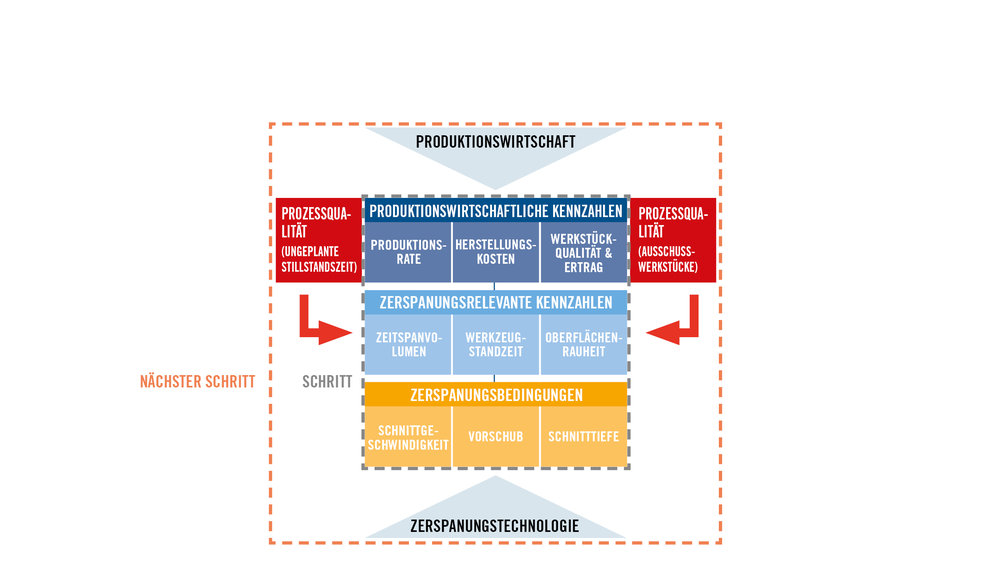
Grundlagen der Produktionswirtschaft
Die Fertigung umfasst eine Reihe von Transformationsprozessen. Über eine Folge einzelner Transformationsschritte wie Schmieden, Schweißen oder Zerspanen werden in einem Betrieb aus Rohmaterialien fertige oder halbfertige Werkstücke hergestellt. Jede Operation basiert auf verschiedenen Elementen. Zu den grundlegenden Elementen der Zerspanung zählen beispielsweise Zerspanungs-werkzeug, Werkzeugmaschine, Spannvorrichtungen und Kühlmittelversorgung. Zusammen bilden diese Elemente ein Zerspanungssystem, das von entsprechenden Betriebsmitteln und Bauteilen in einem Produktionssystem unterstützt wird.
Das Produktionssystem ist in Planungs-, Programmierungs- und betriebswirtschaftliche Funktionen eingebettet. Daraus ergibt sich eine Produktionsumgebung. Das Kernelement einer Produktionsumgebung ist der Mensch. Zwar kommen heutzutage in der Fertigung in großem Stil Computer, Roboter und andere hochentwickelte Technologien zum Einsatz, die Entscheidungen, die diese Umgebung steuern, treffen jedoch Menschen.
Der Zerspanungsprozess beruht auf anwendungstechnischen Details bezüglich Werkzeugauswahl, Zerspanungsbedingungen, Programmierung und Werkstoff sowie Spannvorrichtung. Weitere wesentliche Faktoren sind Produktionsmengenanforderungen und die vorgegebene Qualität fertiger Werkstücke.
Die Verknüpfung anwendungstechnischer Details mit wirtschaftlichen Anliegen wird als Produktionswirtschaft bezeichnet. In der Produktionswirtschaftslehre geht es darum, alle involvierten Faktoren miteinander in Einklang zu bringen. Die technischen Elemente sorgen für die gewünschten Ergebnisse hinsichtlich Werkstückqualität, Quantität und Pünktlichkeit – dabei müssen die Arbeitsschritte allerdings zu Kosten ausgeführt werden, die es dem Unternehmen ermöglichen, wirtschaftlich erfolgreich zu sein.
Um bei der Zerspanung Produktivität und Kosten in Einklang zu bringen, müssen drei Phasen durchlaufen werden. Die erste Phase besteht darin, einen zuverlässigen Zerspanungsprozess zu etablieren. Dabei ist entscheidend, dass unerwartete Ereignisse wie defekte Werkzeuge, unkontrollierte Späne und in der Folge kaputte Werkstücke auf ein Minimum reduziert werden. In einer Werkstatt lässt sich operative Zuverlässigkeit erreichen, indem belastungsfähige Werkzeuge zum Einsatz kommen, die der im Bearbeitungsprozess generierten mechanischen, thermischen, chemischen und tribologischen Beanspruchung gewachsen sind.
Abbildung 2 – In STEP entwickeltes umfassendes Zerspanbarkeitsmodell.
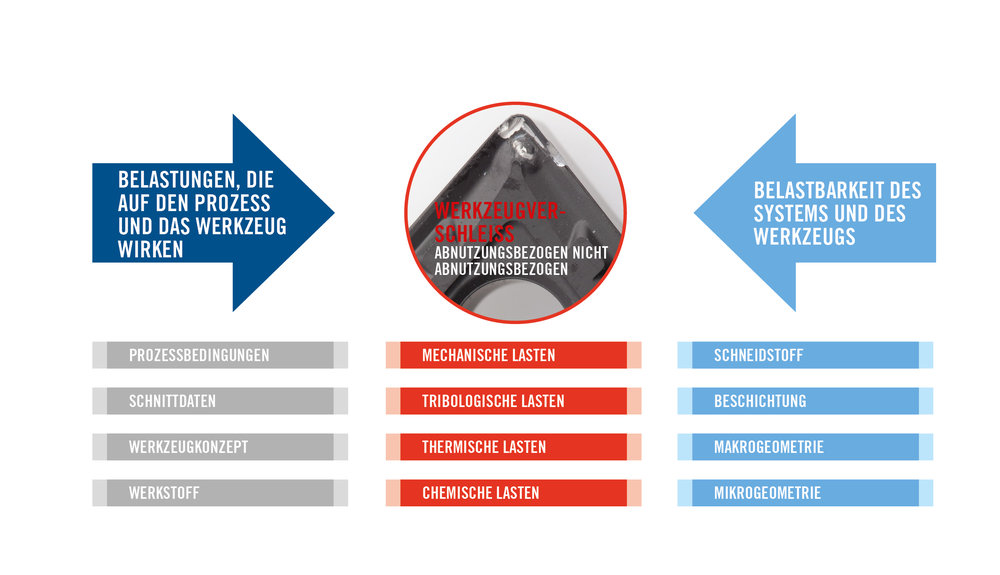
HQ_ILL_Machinability _model
In der zweiten Phase auf dem Weg zu einer ausgewogenen Produktionswirtschaft geht es um die Wahl von Zerspanungsbedingungen, die die Einschränkungen im Bearbeitungsprozess durch die gegebenen Umstände widerspiegeln. Theoretisch sind die Fähigkeiten eines Zerspanungswerkzeugs breit gefächert, in der jeweiligen Werkstattpraxis allerdings ist die Palette effektiver Anwendungsparameter eingeschränkt.
So variieren beispielsweise die Fähigkeiten und die Leistung eines Werkzeugs in Abhängigkeit von der Leistung der Werkzeugmaschine, mit der es angewendet wird, den Zerspanungseigenschaften des Werkstoffs oder der Konfiguration eines Bauteils, das möglicherweise vibrations- oder verzerrungsanfällig ist. Zwar gibt es theoretisch eine große Bandbreite möglicher Zerspanungsbedingungen, doch in der Praxis ist die Auswahl an Bedingungen, die problemlos funktionieren, begrenzt.
Abbildung 3 zeigt eine große Palette bzw. Zahl von Schnittgeschwindigkeiten, Schnitttiefen und Vorschüben, die angesichts verschiedener praktischer Aspekte einer spezifischen Schnittanwendung auf eine kleinere Auswahl begrenzt wurde.
Abbildung 3 – 3D-Illustration, zeigt alle Kombinationen von Zerspanungsbedingungen, die angesichts der Einschränkungen durch die gegebene Zerspanungsumgebung in Frage kommen.

HQ_ILL_Machining_Process_cutting_conditions
Wenn Zerspanungsbedingungen Anwendung finden, die jenseits der Anwendungsbeschränkungen der jeweiligen Situation liegen, hat dies negative wirtschaftliche Auswirkungen, darunter höhere Kosten und eine geringere Produktivität. Wohl 90 Prozent aller Probleme bei der Zerspanung sind darauf zurückzuführen, dass die Beschränkungen, denen der Zerspanungsprozess durch reale Werkstattbedingungen unterliegt, nicht berücksichtigt wurden.
Wenn sich Zerspanungsbedingungen innerhalb der Grenzen bewegen, die durch reale Werkstatt-bedingungen definiert sind, ist die Operation aus technischer Sicht sicher. Doch nicht jede technisch sichere Kombination von Zerspanungsbedingungen führt zu gleichen wirtschaftlichen Ergebnissen. Eine Änderung der Zerspanungsbedingungen hat Auswirkungen auf die Kosten des Zerspanungsprozesses. Durch eine Umstellung auf Zerspanungsbedingungen, die zwar technisch sicher, aber aggressiver sind, wird die Produktion fertiger Werkstücke gesteigert, doch geht ab einem gewissen Punkt die Produktivität zurück, weil die aggressiveren Zerspanungsparameter eine kürzere Werkzeugstandzeit zur Folge haben. Mit der Zeit ist auch der Ausstoß von Teilen rückläufig, weil mehr Zeit auf den Austausch verschlissener Werkzeuge aufgewendet wird.
An einer bestimmten Stelle gibt es eine Kombination von Zerspanungsbedingungen, bei denen Produktionsleistung und Fertigungskosten in Einklang stehen. Abbildung 4 zeigt die Beziehung zwischen Zerspanungsbedingungen, Produktivität und Werkzeug- und Maschinenkosten. (In der Graphik werden nur jene Elemente angezeigt, die bei sich verändernden Zerspanungsbedingungen variieren; Material-, Gemein-, Verwaltungs- und Engineering-Kosten werden nicht berücksichtigt.) Aggressivere Bedingungen sind an der rechten Seite der Achsen dargestellt, eine höhere Produktivität oben. Der hellblaue Streifen in der Mitte der Graphik zeigt, welche Zerspanungsbedingungen ein ausgewogenes Verhältnis von Produktivität (höchster Ausstoß) und Wirtschaftlichkeit (geringste Kosten) bewirken.
Abbildung 4 – Beziehung zwischen Zerspanungsbedingungen, Produktivität und Bearbeitungskosten. Bei dieser Abbildung handelt es sich um ein vereinfachtes Modell ohne Berücksichtigung von Verschwendungsfaktoren.
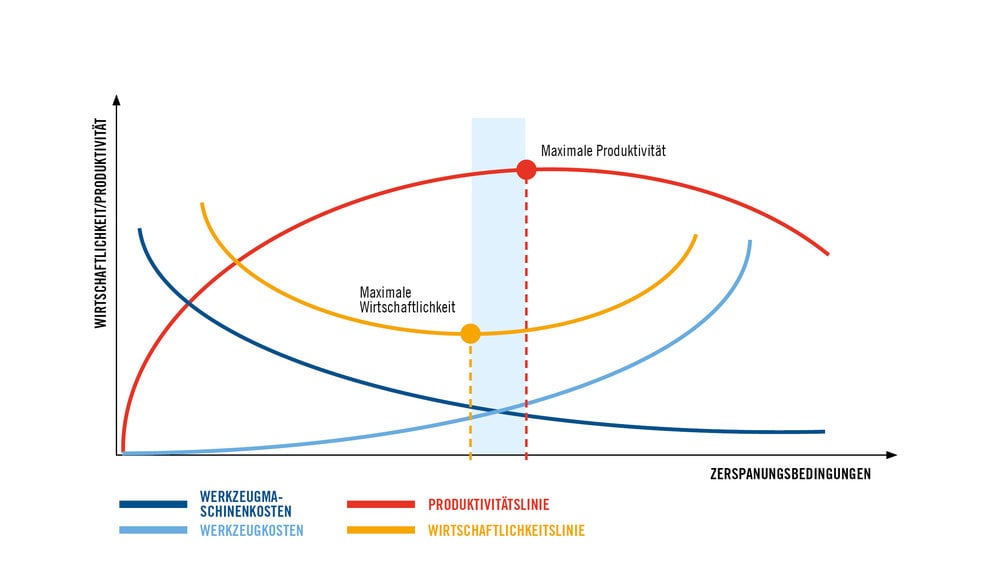
HQ_ILL_Machining_Process_relationship_cutting_conditions_productivity_machining_costs
Dementsprechend geht es in der dritten Phase auf dem Weg zu einer ausgewogenen Produktionswirtschaft darum, die optimale Kombination von Zerspanungsbedingungen für eine bestimmte Situation zu ermitteln. Dabei müssen alle Faktoren im Zerspanungsprozess berücksichtigt werden, damit ein Arbeitsbereich geschaffen werden kann, in dem die Zerspanungsparameter zum gewünschten Maß an Produktivität und Wirtschaftlichkeit führen.
Auswirkungen von Verschwendung auf die Produktionswirtschaft
Unglücklicherweise gibt es einen Faktor, dem die eleganten wissenschaftlichen Methoden der ausgewogenen Produktionswirtschaft im Fertigungssystem ausgeliefert sind: Verschwendung. Sie stört das Gleichgewicht und tritt in vielerlei Formen auf. Beispielsweise kommt es zu einer Energie- und Stromverschwendung, wenn eine 60-kW-Werkzeugmaschine in einer laufenden Anwendung eingesetzt wird, die nur 15 kW erfordert. Wenn gefertigte Werkstücke nicht den erforderlichen Qualitätskriterien genügen, werden auf dem Weg zu diesem nicht akzeptablen Ergebnis Zeit, Geld und Ressourcen, die in den Prozess investiert werden, verschwendet. Gleichermaßen ist auch die Herstellung von Werkstücken, die das erforderliche Maß an Qualität unnötig übertreffen, unwirtschaftlich, weil mit dem Erreichen einer höheren Qualität auch die Kosten steigen.
Weniger bekannt und zugleich unterschätzt ist die Verschwendung, die mit der Nichtausschöpfung oder dem falschen Einsatz intellektueller Ressourcen einhergeht. Bestimmte Mitarbeiter in einem Unternehmen können über Kenntnisse oder Fertigkeiten verfügen, die dem Unternehmen beim Erreichen seiner Ziele helfen könnten, doch aus Gründen, die von schlechter Kommunikation bis hin zur Firmenpolitik reichen können, werden solche Kenntnisse und Fertigkeiten nicht weitergegeben und somit nicht genutzt.
Mittel zur Verschwendungsreduktion
Nachdem Verschwendung erkannt und kategorisiert wurde, sollte ein Betrieb einen Plan ausarbeiten, um sie zu reduzieren oder ganz zu beseitigen. Damit ein Hersteller unwirtschaftliche Praktiken lokalisieren, beziffern und minimieren kann, stehen ihm verschiedenste Mittel zur Verfügung. Beispielsweise können durch die Analyse der Verwendung, Manipulation und Alterung von Werkzeugen Problembereiche herausgearbeitet werden.
Solche Analysen haben ergeben, dass in einigen Fällen ganze 20 bis 30 Prozent der Werkzeuge, die von Mitarbeitern als verschlissen definiert wurden, in Wirklichkeit noch einsatzfähig waren – die verbleibende Werkzeugstandzeit wurde also verschwendet. Wenn eindeutige Kriterien für den Werkzeugverschleiß eingeführt und die entsprechenden Standards dem Betriebspersonal mitgeteilt werden, kann die verschwendete Werkzeugstandzeit erheblich reduziert werden.
Gleichermaßen kann durch die Analyse von Maschinenstillstandszeiten die Zeit beziffert werden, die auf Tätigkeiten wie Einstellung, Programmierung und Werkzeugwechsel verwendet wird. Solche Analysen zeigen häufig, dass sich ganze 50 bis 60 Prozent an Maschinenausfällen durch besseres Kenntnis, Durchführung und Koordination dieser notwendigen, aber zeitintensiven Tätigkeiten vermeiden ließen.
Mithilfe von Interviews, Umfragen und Schulungsprogrammen können zahlreiche nützliche Informationen im Hinblick auf personalbezogene Probleme offengelegt werden, die zur Verschwendung intellektueller Ressourcen und nicht genutzter Kenntnisse und Fertigkeiten führen. In der Folge leisten Mitarbeiter bessere Arbeit und entwickeln Fähigkeiten, die die Personalproduktivität steigern.
Management wertschöpfender, stützender und nicht wertschöpfender Tätigkeiten
Anfang des 20. Jahrhunderts untersuchte der US-amerikanische Prozessingenieur Fredrick Taylor die Arbeitsschritte in einer Werkstatt und schlug dann vor, Produktivitätssteigerungen durch den Verzicht auf alle Tätigkeiten in einem Prozess zu erreichen, die den Wert des Endprodukts nicht steigern. Moderne Fertigungsvorgaben für eine „schlanke Produktion“ folgen diesem Denkansatz.
In Zerspanungsprozessen tritt die einzige wertschöpfende Tätigkeit dann auf, wenn das Werkzeug tatsächlich Metall zerspant und Späne produziert. Weitere Tätigkeiten wie die Zufuhr und Einspannung von Teilen, die als Stützleistungen bezeichnet werden, steigern nicht direkt den Wert des hergestellten Produkts, sind aber erforderlich, damit die wertschöpfende Tätigkeit stattfinden kann.
Eine dritte Gruppe von Tätigkeiten im Zerspanungssystem sind jene, die eigentlich überflüssig sind. Diese schaffen weder einen Mehrwert noch ermöglichen sie die Wertschöpfung. Stattdessen verbrauchen sie ohne jeden Nutzen Ressourcen, sind also reine Verschwendung. Eine unnötige Aktivität ist beispielsweise die Problemlösung. Wenn ein Prozess von Anfang an sachgerecht ausgelegt und kontrolliert wird, treten keine Probleme auf und für ihre Lösung muss keine Zeit verschwendet werden.
Abbildung 5 – Schematische Darstellung einer Zerspanungswerkstatt und aller damit verbundenen Elemente.
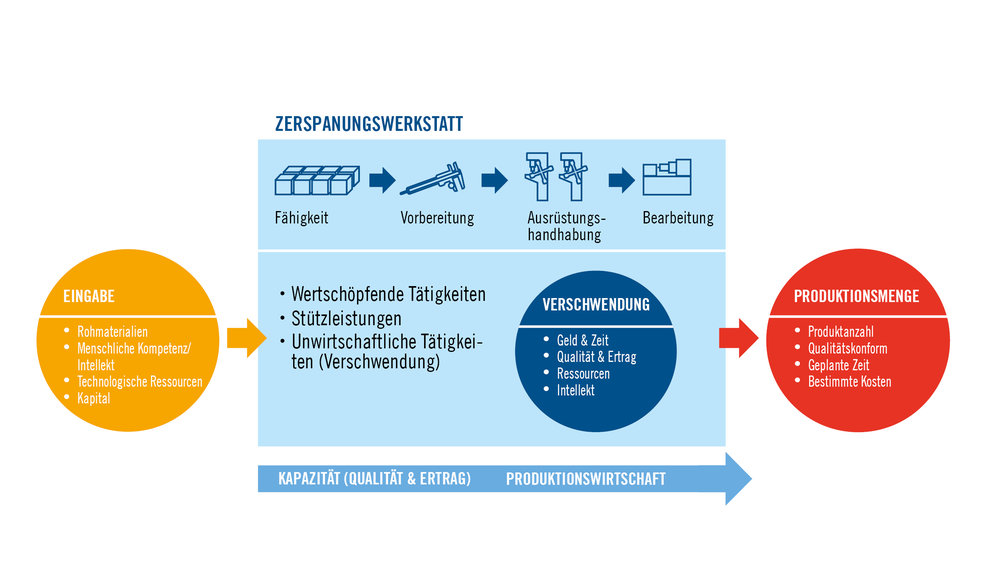
Fazit
In der Vergangenheit wurden nicht erforderliche Tätigkeiten lange Zeit als Teil des Herstellungsprozesses akzeptiert und nicht als erhebliche Störfaktoren beim Erreichen einer ausgewogenen Produktionswirtschaft erkannt. Heute verlagert sich die Aufmerksamkeit auf die Beseitigung oder Minimierung unnötiger Tätigkeiten. Der Fokus bei der Produktivitäts- bzw. Kapazitätsplanung liegt auf der Beseitigung unnötiger Tätigkeiten, der Minimierung von Stützleistungen und der Optimierung wertschöpfender Tätigkeiten. (Siehe Abbildung 6)
Abbildung 6 – Übersicht über wertschöpfende Tätigkeiten (orange), Stützleistungen (blau) und unwirtschaftliche Tätigkeiten (rot). Der menschliche Faktor (grau) ist der Schlüsselfaktor, um produktionstechnische Spitzenleistungen optimal zu erreichen.
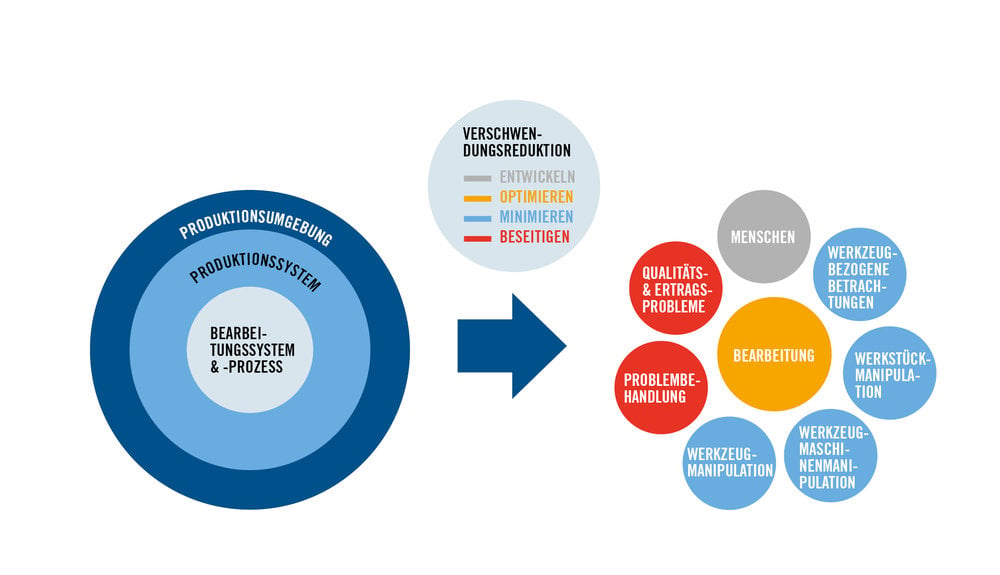
HQ_ILL_Machining_system_process
Mit der Beseitigung von Verschwendung wird die theoretische zur praktischen Produktionswirtschaft. An dieser Stelle können die Fortschritte in der Produktionswirtschaft direkt für den Erfolg des Unternehmens angewendet werden. Allerdings ist bei den Bemühungen zur Beseitigung aller Verschwendungsanlässe Vorsicht geboten. Bei verschwendungsreduzierenden Maßnahmen ist es wichtig, die Kapitalrendite zu bestimmen. Um einen bestimmten Verschwendungsfaktor komplett zu beseitigen, könnte eine derart umfangreiche Investition erforderlich sein, dass es aus wirtschaftlicher Sicht sinnvoller sein könnte, die Verschwendung ganz oder teilweise zu akzeptieren und damit zu leben. Entscheidungen dieser Art werden nach einer geeigneten quantitativen Analyse sowie betriebsinternen Gesprächen über die Auswirkungen von Entscheidungen auf Ziele und Philosophie des Unternehmens getroffen.
Kasten:
Seco Consultancy Services
Im Zuge der Weiterentwicklung von Fertigungsprodukten benötigen Benutzer zunehmend Anwendungs-hilfen, um neue Technologien so nutzbringend wie möglich einzusetzen. Im Bereich der Zerspanung besteht diese Hilfe zunächst in der Beratung bei der Auswahl des richtigen Werkzeugs für einen bestimmten Arbeitsschritt. Nachdem die Entscheidung für ein Werkzeug gefallen ist, ermöglichen weitere Informationen die Entscheidung für optimale Zerspanungsbedingungen, den Einsatz des Kühlmittels und andere Überlegungen. Wenn dann ein Werkzeug in diesem Arbeitsschritt nicht wie erwartet funktioniert, kann der Werkzeuglieferant Hilfestellung bei der Problemlösung geben. Diese drei Arten der Unterstützung machen einen traditionellen Werkzeug-Service aus.
Wenn sich ein Werkzeug-Service von einer einzelnen Anwendung auf einen Prozess ausweitet, in dem ein Werkstück mehrere Arbeitsschritte an einer oder mehreren Maschinen durchläuft, benötigen Endkunden Unterstützung bei der Einrichtung der Abfolge von Arbeitsschritten, der Werkstückmanipulation und weiteren Faktoren, um Effizienz und Produktivität zu maximieren. Diese Art der Unterstützung lässt sich als technischer Service bezeichnen.
Immer öfter kommt es vor, dass Hersteller nach einer Orientierung bei der Verbesserung von Funktionen, Ausstoß und Kostenkontrolle für einen gesamten Betrieb oder ein Unternehmen suchen. Für solche Fälle gibt es einige unabhängige Beratungsfirmen, die eine von ihnen als Management- oder Fertigungsberatung bezeichnete Unterstützung anbieten. Um jedoch eine Fertigungsorganisation wirklich beurteilen zu können, ist es unabdingbar, die Kernprozesse des Geschäftsbetriebs voll und ganz zu verstehen.
Unter Einsatz seiner jahrelangen und weitreichenden Kenntnisse von Zerspanungsprozessen und Werkzeuglösungen bietet Seco bereits seit Jahrzehnten sowohl einen traditionellen Werkzeug-Service als auch einen technischen Service sowie umfassendere Beratungsleistungen an. Diese Dienstleistungen wurden zunächst gelegentlich bzw. situationsbedingt zur Verfügung gestellt, bis Seco seine Beratungsdienste 2016 mit Seco Consulting Services professionalisierte, um seinen Kunden ein Spektrum optimierter und besser angepasster Fertigungsdienstleistungen anzubieten.
Seco Consulting Services umfasst ein breites Spektrum an speziellen Ressourcen und Leistungen. Werkzeugauswahl und Anwendungshilfe sind rund um die Uhr online verfügbar, um die unmittelbaren Produktivitätsbedürfnisse in der Werkstatt zu erfüllen.
Technische Serviceleistungen können zunächst über elektronische Kommunikation erfolgen, bei Bedarf folgt ein Besuch vor Ort. Seco Consulting Services können auch umfassende Analyse- und Beratungsleistungen einschließen, die jeden Arbeitsschritt in einer Werkstatt berücksichtigen. Diese Serviceleistungen können Beratungen zur Werkzeugmaschineninstandhaltung, Werkstattgestaltung, Logistik und organisatorischen Funktionen umfassen. Auch Hinweise zu Problemen in Bezug auf Fertigkeiten und Kenntnisse von Mitarbeitern und zur Beziehung der auf die Produktionsstrategien des Unternehmens angewendeten Herstellungstechniken und Kostenüberlegungen können Gegenstand von Beratungen sein.
Jede Beratungsbeziehung mit Seco Consultancy basiert auf dem Konzept NEXT STEP, wird aber zudem genau auf die spezifischen Bedürfnisse des beteiligten Unternehmens zugeschnitten und ist ein Dialog zwischen Seco und dem Kunden, der darauf ausgerichtet ist, ein gemeinsames Ziel zu erreichen.
Fordern Sie weitere Informationen an…