www.konstruktion-industrie.com
30
'09
Written on Modified on
Höhere Qualität und niedrigere Kosten beim Schweißen von beschädigten Eisenbahnschienen
Tata Steel Rail hat ein neuartiges Schweißverfahren entwickelt, mit dem sich einzelne Schäden auf der Lauffläche von Eisenbahnschienen deutlich wirtschaftlicher reparieren lassen. Der wesentliche Vorteil des neuen Verfahrens ist der Ersatz des konventionellen Lichtbogen-Handschweißens mit seinen häufigen und großen Qualitätsschwankungen durch automatisierte und besser kontrollierbare Arbeitsabläufe. Das halbautomatische Verfahren nutzt das offene Lichtbogenschweißen mit flussmittelgefüllter Drahtelektrode und erfordert lediglich eine niedrige Vorwärmtemperatur zur Steuerung der metallurgischen Veränderungen in der Wärmeeinflusszone. Angesichts der hohen Kosten für die Reparatur oder den Austausch von beschädigten Schienenstücken von mehreren Tausend Euro und der zunehmenden Häufigkeit von Schienenschäden durch den anwachsenden Verkehr auf den meisten Schienenstrecken liegt die hohe Bedeutung des neuen Verfahrens auf der Hand. Das Verfahren wurde sorgfältig getestet, und derzeit fertigt der Hersteller ein erstes Gerät für Vor-Ort-Einsätze auf mehreren europäischen Schienennetzen, darunter in Frankreich und Großbritannien.
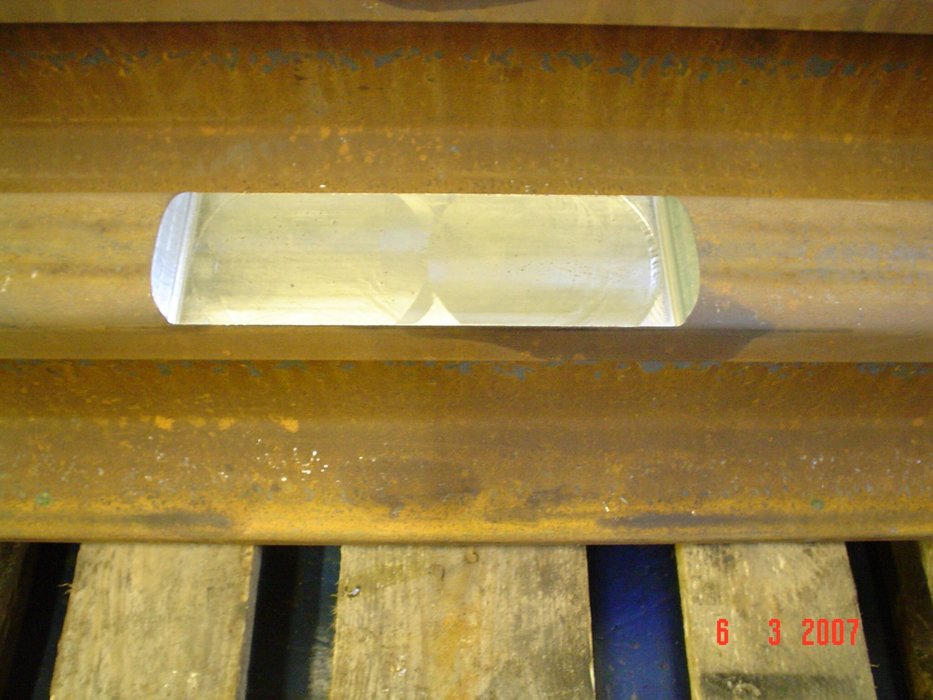
Ein Ersatz solcher Schadstellen durch aluminothermisch verschweißte kurze Schienenstücke ist teuer und bringt zudem durch die Schweißnähte zwei neue Unregelmäßigkeiten in die Lauffläche, wodurch die Vorteile der warmgewalzten, bis zu 120 Meter langen Schienenstücke verloren gehen. Das konventionelle Alternativverfahren zur Reparatur solcher Schäden ist das manuelle Lichtbogenschweißen, das in zahlreichen Industriebereichen zum Einsatz kommt. Diese Technik ist jedoch zeitaufwändig und in hohem Maße abhängig von den individuellen Fähigkeiten des Schweißers. Außerdem verursacht sie oft interne Schädigungen, wie etwa Porositäten, die zu Materialermüdung und Schienenbrüchen führen, sofern sie nicht rechtzeitig durch eine Ultraschalluntersuchung entdeckt werden.
Die Wirtschaftlichkeit und technische Stabilität des neu entwickelten Verfahrens beruht im Wesentlichen auf drei Faktoren:
1. Die geringe Vorwärmtemperatur von 800 Grad Celsius anstelle von 3.500 Grad beim konventionellen Verfahren verkürzt den Zeitaufwand, verringert die Tiefe der Wärmeeinflusszone und führt zu einer stabileren Feinstruktur des Stahls.
2. Die standardisierte Entfernung der beschädigten Bereiche mit einer gesteuerten Fräse hat den Vorteil der Reproduzierbarkeit und ist unabhängig von dem subjektiven Urteil des Bedieners.
3. Das Verfahren des halbautomatischen, programmierten offenen Lichtbogenschweißens mit flussmittelgefüllter Drahtelektrode gewährleistet eine Kontrolle des Wärmeeintrags sowie berechenbare Einsatzzeiten.
Das neu entwickelte Verfahren stellt eine hohe Güte der wiederhergestellten Lauffläche sicher, weil die instandgesetzten Bereiche extrem ermüdungsfest sind und zudem eine ähnliche Verschleißfestigkeit aufweisen wie der bewährte Schienenwerkstoff R 260 mit einer einheitlichen Härte und Feinstruktur entlang den geschweißten Bereichen.
Die neue patentierte Reparaturtechnik von Tata Steel umfasst vier Schritte: Zunächst wird die Schadstelle mit einer tragbaren Drei-Achs-Schienenfräse entfernt, die seitlich an der Schiene eingespannt wird. Dies gewährleistet eine einheitliche Formgebung des entnommenen Bereichs und ist schon damit eine deutliche Verbesserung im Vergleich zum manuellen Schleifen oder Flämmen, mit denen sich keine gleichmäßige Oberflächenstruktur und keine einheitlich geformten Hohlräume erreichen lassen, die den automatisierten Schweißprozess erleichtern.
Als nächstes werden die angrenzenden Bereiche sowie der Hohlraum mit einem konventionellen Brenner vorgewärmt. Die Wahl des Temperaturbereichs dient dabei der Kontrolle des Mikrogefüges des Stahls in der Wärmeeinflusszone. Der programmierte gitterförmige Auftrag der Schweißnähte gewährleistet, dass das Microgefüge des Schienenstahls feinperlitisch bleibt, ohne Anteile aus sprödem Martensit. Für Schienen aus R 260 liegt die vorgeschriebene Temperatur hierfür zwischen 60 und 80 Grad Celsius. Dieser Temperaturbereich eignet sich für die große Mehrheit der kohlenstoffreichen Stahlwerkstoffe, die heute für Schienen im Einsatz sind. Für Stahlsorten mit einer deutlich anderen Übergangscharakteristik, wie etwa kohlenstoffarme karbidfreie bainitische Stähle, müsste die optimale Vorwärmtemperatur eventuell angepasst werden.
Der dritte Schritt nutzt ein halbautomatisches Reparatur-Schweißgerät nach dem Prinzip des offenen Lichtbogenschweißens mit dem vom englischen Schienennetzbetreiber Network Rail zugelassenen Schweißzusatz TN3-0 unter vorgeschriebenen Schweißparametern. Maßgeblich dafür, dass keine neue Wärmeeinflusszone entsteht, ist dabei die Positionierung der obersten Schweißschicht. Der größte Teil dieser obersten Schweißschicht wird beim nachfolgenden Profilschleifen entfernt.
Im vierten und letzten Schritt wird mit einer konventionellen Schienenschleifmaschine das Längs- und Querschnittsprofil der Schiene wiederhergestellt und angepasst.
Eine vergleichende Untersuchung des Temperaturverlaufs bei dem neuen Verfahren gegenüber der bekannten Technik des Lichtbogen-Handschweißens mit Hilfe von eingeschlossenen Thermoelementen ergab mehrere Tatsachen, die die hohe metallurgische Stabilität des Prozesses bestätigen:
– Trotz der geringen Vorwärmung auf lediglich 80 Grad Celsius bleibt die Temperatur in der Wärmeeinflusszone nach jedem Auftrag einer Schweißnaht oberhalb von 200 Grad, was eine Umwandlung in ein martensitisches Gefüge verhindert (die beim Schienenstahl R 260 erst unterhalb von 160 Grad Celsius beginnt) .
– Die Abkühlungsgeschwindigkeit liegt bei dem neuen Verfahren nahezu identisch zum konventionellen Handschweißen. Dies gilt für jede aufgetragene Schicht mit Ausnahme der ersten Lage, wo eine höhere Abkühlungsrate von 5,2 °C/s auftritt. Auch diese Abkühlungsrate liegt jedoch nur bei der Hälfte des kritischen Werts für die Umwandlung zu Martensit.
– Die Rissfreiheit der Schweißnaht wird ersichtlich durch das vollständig perlitische Gefüge ohne Bereiche aus Martensit oder Bainit.
– Der Härteverlauf zeigt, dass die Abriebfestigkeit des bainitischen Schweißgutes vergleichbar ist mit der des Grundwerkstoffs R 260 und damit ein einheitliches Längsprofil dauerhaft gewährleistet.
In Biegeschwingversuchen mit einer Belastung, die dem Dreifachen der im Einsatz zu erwartenden Werte entspricht, ertrug die Schweißnaht fünf Millionen Zyklen ohne jeden Ausfall. Weitere 4,3 Millionen Zyklen überstand dieselbe Schweißnaht zudem unter einer Belastung mit dem Achtfachen der Einsatzlast.
Fordern Sie weitere Informationen an…