www.konstruktion-industrie.com
12
'10
Written on Modified on
High-Speed Fiber-Bestückung auf großen und komplexen Strukturen
Um die Effizienz des Kraftstoffverbrauchs bei Flugzeugen steigern zu können, ist eine Gewichtsreduzierung von wesentlicher Bedeutung. Eine höhere Leistungsfähigkeit ist nicht nur in Bezug auf die Kosten unerlässlich, sondern auch wegen der immer größer werdenden Entfernungen, die Flugzeuge zukünftig zurücklegen werden. Das gute Verhältnis von Festigkeit zu Gewicht von Carbonfasern ist eine der wichtigsten Innovationen der Gegenwart. Die geforderten hohen Produktionsraten bei der Herstellung von Flugzeugteilen erfordern jedoch äußerst komplexe Maschinen. Electroimpact entwickelte eine herausragende Lösung, die eine automatisierte Fiber-Bestückung bei Geschwindigkeiten von 2000 Inch pro Minute (50 Meter pro Minute) ermöglicht. Diese Lösung erfordert ein äußerst ausgeklügeltes Steuerungssystem und sehr stabile und präzise Achsantriebssysteme. Andantex, USA, lieferte für den Antrieb der Achsen sämtliche kritischen, mechanischen Komponenten.
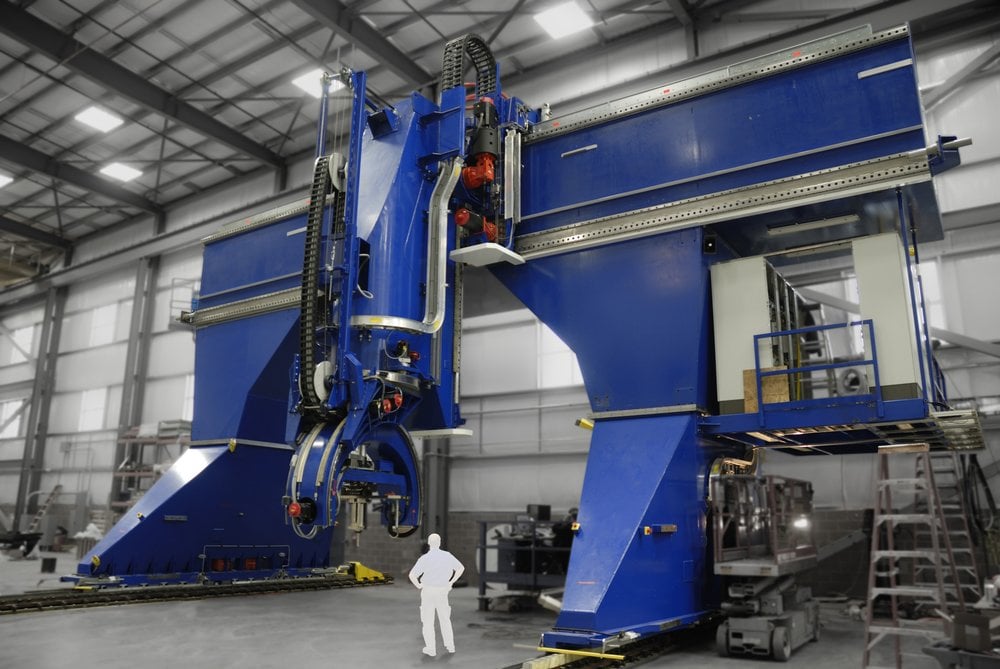
Electroimpact ist ein junges Ingenieur-getriebenes Unternehmen, mit der Vision, der führende Anbieter von automatisierten Anlagen für die weltweite Luftfahrtindustrie zu werden. Electroimpact hat eine automatisierte Fiber-Bestückungs (AFP)-Technologie entwickelt, die das Schneiden und Aufbringen von Kohlefaser-Streifen in vom Kunden vorgegebenen Toleranzbereichen von bis zu 2000 IPM über schräge, komplexe Oberflächen ermöglicht. Alle Laminierungen können vollständig bidirektional ausgeführt werden, bei voller Kontrolle des Bedieners über den Vorschub und ohne Auswirkung auf die Endgenauigkeit des Schnittes. Electroimpact ist ein sehr erfahrener Lösungsanbieter im Bereich Fabrikautomation und Werkzeugmaschinen. Die besondere Stärke des Unternehmens liegt in der Integration von Automatisierungstechnik und Werkzeugmaschinen in synergistische Produktionslösungen. Ein hochqualifiziertes und flexibles Entwicklungsteam ist in der Lage, mehrere Großprojekte gleichzeitig zu bearbeiten. Dieser einzigartige Ansatz hat dazu geführt, dass sich Electroimpact zum weltweit größten Integrator von Montagelinien für die Luftfahrtindustrie entwickelte. Zu den Kunden zählen zivile und militärische Flugzeughersteller auf der ganzen Welt. Der jüngste Kunde ist ein großer US-Flugzeugkomponentenhersteller. Dieser fertigt Rümpfe, Unter-Flügel-Komponenten, Verbundwerkstoffe und Tragflügel für die Luftfahrtindustrie. Der Hauptsitz des Unternehmens befindet sich in Wichita, Kansas, der weltweiten Hauptstadt für Luftfahrt. Weitere Betriebe sind in Tulsa und McAlester, Oklahoma, in Prestwick, Schottland und Samlesbury, England.
Die automatisierte Fiber-Bestückungsmaschine (AFP) wurde für die Produktion großer Verkehrsflugzeug-Konstruktionen entworfen. Sie ist voll modular; Werkzeugköpfe werden innerhalb von 30 Sekunden vollautomatisch gewechselt. Die Bearbeitung dieser großen Teile der Luft- und Raumfahrtindustrie erfordert ein stabiles Maschinengestell, aus diesem Grund wiegt die Maschine, die die X-, Y-und Z-Bewegung des Faser-Bestückkopfs (Post Mill oder Gantry Modelle) steuert, 350.000 Lbs (175 Tonnen) und wird auf 0,2 g beschleunigt. Über CarbonFaser-Schlepplifte (schmale, imprägnierte Kohlefaserstreifen), die auf demselben Bauelement in vielfältigen Materialarten aufgebracht werden können (1/4»- oder 1/8»-breite Schlepplifte für Bereiche mit hoher Kontur. ½» oder breiter für geringere Profilflächen), wird eine größtmögliche Produktivität erreicht: kein Drall (100 %), kein Spleißbruch (100 %) sowie vollständig bidirektionaler Betrieb. Die X-, Y-, Z- und die Zylinder-Drehachsen arbeiten zusammen, damit die Carbonfaser die Kontur des zu fertigenden Bauteils nachvollziehen kann. Die Carbonfaser-Schlepplifte werden so auf dem Werkzeug platziert, dass sie dem zu fertigenden Bauteil bis zur endgültigen Form folgen können. Darüber hinaus kommt die Carbonfaser bei verschiedenen Schichten und unterschiedlichen Anordnungen zum Einsatz, um die Stärke des endgültigen Bauteils zu optimieren. Carbonfaser hat eine hohe Spannung, deshalb müssen sämtliche darauf befindlichen Lasten in der Spannung unterstützt werden. Die Gesamthübe der X-Achse können variieren von 2 Metern (6.6 Ft.) bis hin zur vollen Länge der X-Achse von 30 Metern (98,4 Ft.). Der Arbeitsweg (Hub) hängt ab von dem zu fertigenden Teil.
Ein fortschrittliches Steuerungssystem
Diese Maschine beinhaltet ein komplettes Re-Engineering der Schneidanlage und eine Optimierung des Beschickungssystems, der Schleppliftbahn sowie des Spulengestells des Fiber-Bestückkopfes. Die Steuerung der Maschine ermöglicht in-spec- und on-the-fly-Schneidevorgänge bei 2000 IPM und darüber hinaus. Insbesondere beim High-Speed-Schneiden on-the-fly tauchten einige Fragen auf. Mit einer Ausbringung von 2000 IPM (R) und einer maximalen Schneideeinstellungsstoleranz von + / -0,050 "(oder insgesamt 0,10" [k]), ist das Zeitintervall folgendes:
T = (60 * k) / R (Sekunden) oder,
T = (60 * 0.10) / 2000T = 0.003 Sekunden.
Mit anderen Worten, bei 2000 IPM entspricht eine Millisekunde einer Vorwärtsbewegung des Schlepplifts in etwa 0,033 Zoll. Dies verdeutlicht, dass die Gesamtgenauigkeit sowie die Wiederholgenauigkeit des Schneid-Systems um einiges höher sein müssen als die einer typischen CNC-Abtastrate (4 bis 8 ms). Die Wiederholgenauigkeit einzelner Komponenten (.z.B. Antriebe, Ventile, etc.) muss im Bereich unter einer Millisekunde liegen oder darunter. Weiterhin muss das System für die Signalisierung der Schnitte eine Auflösung im Bereich unter einer Millisekunde aufweisen. Electroimpact entwickelte einen High-Speed-Schneidemechanismus, der ein Schneiden bei hohen Geschwindigkeiten ermöglicht, mit Schneidezeiten von unter einer Millisekunde. Die äußerst geringen Abweichungen dieses Systems ermöglichen sehr hohe Wiederholgenauigkeiten und Geschwindigkeiten bei der Bestückung. Zu den Faktoren, die die Zeitintervalle des on-the-fly Schneide- und Bestückvorgangsvorgangs beeinflussen, gehören die Programmausführung, die Reaktion des Ausgangsmoduls, Betätigung des Magnetventils, Reaktionen der Aktoren auf Luftströmung und Trägheitskräfte etc. Jeder dieser Faktoren kann eine Verzögerung bei der Ausführung eines Schnittes oder des Soll-Signals hervorrufen. Ist die Verzögerung vorhersehbar und wiederholbar, kann der Schnitttakt kompensiert werden. Wo es möglich ist, müssen solche Verzögerungen minimiert werden. Dank umfangreicher Entwicklungen und Tests bei Electroimpact konnten die Abweichungen und Verzögerungen bei der Bestückung und beim Schneiden verringert werden auf unter eine Millisekunde, so dass sehr genaue Bestückungs- und Schneidevorgänge bei hohen Geschwindigkeiten möglich sind. Konventionelle Steuerungen wie beispielsweise Speicherprogrammierbare Steuerungen oder CNC-Steuerungen arbeiten in der Regel mit einer "Abtastrate" im Millisekundenbereich.
Die automatisierte Fiber-Bestückungsmaschine (AFP) wurde für die Produktion großer Verkehrsflugzeug-Konstruktionen entworfen. Sie ist voll modular; Werkzeugköpfe werden innerhalb von 30 Sekunden vollautomatisch gewechselt. Die Bearbeitung dieser großen Teile der Luft- und Raumfahrtindustrie erfordert ein stabiles Maschinengestell, aus diesem Grund wiegt die Maschine, die die X-, Y-und Z-Bewegung des Faser-Bestückkopfs (Post Mill oder Gantry Modelle) steuert, 350.000 Lbs (175 Tonnen) und wird auf 0,2 g beschleunigt. Über CarbonFaser-Schlepplifte (schmale, imprägnierte Kohlefaserstreifen), die auf demselben Bauelement in vielfältigen Materialarten aufgebracht werden können (1/4»- oder 1/8»-breite Schlepplifte für Bereiche mit hoher Kontur. ½» oder breiter für geringere Profilflächen), wird eine größtmögliche Produktivität erreicht: kein Drall (100 %), kein Spleißbruch (100 %) sowie vollständig bidirektionaler Betrieb. Die X-, Y-, Z- und die Zylinder-Drehachsen arbeiten zusammen, damit die Carbonfaser die Kontur des zu fertigenden Bauteils nachvollziehen kann. Die Carbonfaser-Schlepplifte werden so auf dem Werkzeug platziert, dass sie dem zu fertigenden Bauteil bis zur endgültigen Form folgen können. Darüber hinaus kommt die Carbonfaser bei verschiedenen Schichten und unterschiedlichen Anordnungen zum Einsatz, um die Stärke des endgültigen Bauteils zu optimieren. Carbonfaser hat eine hohe Spannung, deshalb müssen sämtliche darauf befindlichen Lasten in der Spannung unterstützt werden. Die Gesamthübe der X-Achse können variieren von 2 Metern (6.6 Ft.) bis hin zur vollen Länge der X-Achse von 30 Metern (98,4 Ft.). Der Arbeitsweg (Hub) hängt ab von dem zu fertigenden Teil.
Ein fortschrittliches Steuerungssystem
Diese Maschine beinhaltet ein komplettes Re-Engineering der Schneidanlage und eine Optimierung des Beschickungssystems, der Schleppliftbahn sowie des Spulengestells des Fiber-Bestückkopfes. Die Steuerung der Maschine ermöglicht in-spec- und on-the-fly-Schneidevorgänge bei 2000 IPM und darüber hinaus. Insbesondere beim High-Speed-Schneiden on-the-fly tauchten einige Fragen auf. Mit einer Ausbringung von 2000 IPM (R) und einer maximalen Schneideeinstellungsstoleranz von + / -0,050 "(oder insgesamt 0,10" [k]), ist das Zeitintervall folgendes:
T = (60 * k) / R (Sekunden) oder,
T = (60 * 0.10) / 2000T = 0.003 Sekunden.
Mit anderen Worten, bei 2000 IPM entspricht eine Millisekunde einer Vorwärtsbewegung des Schlepplifts in etwa 0,033 Zoll. Dies verdeutlicht, dass die Gesamtgenauigkeit sowie die Wiederholgenauigkeit des Schneid-Systems um einiges höher sein müssen als die einer typischen CNC-Abtastrate (4 bis 8 ms). Die Wiederholgenauigkeit einzelner Komponenten (.z.B. Antriebe, Ventile, etc.) muss im Bereich unter einer Millisekunde liegen oder darunter. Weiterhin muss das System für die Signalisierung der Schnitte eine Auflösung im Bereich unter einer Millisekunde aufweisen. Electroimpact entwickelte einen High-Speed-Schneidemechanismus, der ein Schneiden bei hohen Geschwindigkeiten ermöglicht, mit Schneidezeiten von unter einer Millisekunde. Die äußerst geringen Abweichungen dieses Systems ermöglichen sehr hohe Wiederholgenauigkeiten und Geschwindigkeiten bei der Bestückung. Zu den Faktoren, die die Zeitintervalle des on-the-fly Schneide- und Bestückvorgangsvorgangs beeinflussen, gehören die Programmausführung, die Reaktion des Ausgangsmoduls, Betätigung des Magnetventils, Reaktionen der Aktoren auf Luftströmung und Trägheitskräfte etc. Jeder dieser Faktoren kann eine Verzögerung bei der Ausführung eines Schnittes oder des Soll-Signals hervorrufen. Ist die Verzögerung vorhersehbar und wiederholbar, kann der Schnitttakt kompensiert werden. Wo es möglich ist, müssen solche Verzögerungen minimiert werden. Dank umfangreicher Entwicklungen und Tests bei Electroimpact konnten die Abweichungen und Verzögerungen bei der Bestückung und beim Schneiden verringert werden auf unter eine Millisekunde, so dass sehr genaue Bestückungs- und Schneidevorgänge bei hohen Geschwindigkeiten möglich sind. Konventionelle Steuerungen wie beispielsweise Speicherprogrammierbare Steuerungen oder CNC-Steuerungen arbeiten in der Regel mit einer "Abtastrate" im Millisekundenbereich.
Die Outputs werden einmal pro Abtastung betätigt, wodurch die zeitliche Auflösung der Scan-Zeit limitiert wird. Eine Verzögerung von einer Millisekunde hätte einen Fehler von 0,033» bei der Bestückung zur Folge, was 2000" / Minute entspricht und einen Regelungsfehler von einer Millisekunde nach sich ziehen würde; für High-Speed on-the-fly-Schneidevorgänge wäre dies inakzeptabel. Ein extrem fest sitzender Einbau der CNC-Motion-Steuerung und eine gute zeitliche Koordination der Bestück- und Schneidevorgänge sind ein Muss, um Zeitverzögerungen bei der Ansteuerung zu minimieren.
Electroimpact hat sich für das "Customer Board" von Fanuc entschieden; ein System, das es Electroimpact erlaubt, Schneide- und Bestückvorgänge in das Bewegungsprofil auf der Geschwindigkeits-Befehlsebene der CNC-Maschine zu interpolieren. Dies ist die erste Implementierung des Customer Boards außerhalb Japans. Electroimpact arbeitete eng mit Fanuc zusammen, um die speziellen Features für AFP-Anwendungen zu implementieren. Die von der Steuerung induzierten zeitlichen Verzögerungen liegen im Bereich von Mikrosekunden. Dies eliminiert effektiv Steuerungsverzögerungen als Fehlerquelle beim Schneiden- und Bestücken. Electroimpact-Kunden haben den Bedarf für Programmier-Software, bereitgestellt von einem industrieweit anerkannten Software-Lieferanten, erkannt. Die Software wird als Teil einer Standard-Suite regelmäßig aktualisiert und gepflegt. Seit über zwei Jahren hat Electroimpact eine nicht-exklusive Partnerschaft mit CGTech. Die Unternehmen entwickeln gemeinsam AFP-Programmier-Software unter dem Namen "Vericut Composite-Programmierung und Simulation Suite".
Die einzigartige Lösung von ANDANTEX
Für Electroimpact stellte sich ANDANTEX USA den schwierigsten Bedingungen: Einer Kombination aus hohen Geschwindigkeiten, verbunden mit dem großen Gewicht der Maschinen und sehr komplexen Bewegungsabläufen mit häufigen Beschleunigungen in sämtliche Richtungen. "Wir haben uns für Andantex entschieden, weil niemand sonst in der Lage ist, eine Präzisionslösung in diesem Drehmoment- und Schub-Bereich zu realisieren", erklärt Peter Vögeli, leitender Ingenieur bei Electroimpact, Inc.
Die erste Aufgabe besteht darin, das Flankenspiel zu beseitigen. TwinDRIVE Zahnstangenritzel-Antriebssysteme bestehen aus zwei parallel montierten Servo-Planetengetrieben und Reduzierflanschen, die elektrisch gekoppelt sind. Dieses Vorspann-System eliminiert das Flankenspiel und ermöglicht dem Servo-System eine präzise Ansteuerung der Achspositionen.
Die zweite Aufgabe besteht darin, eine sehr hohe Steifigkeit zu gewährleisten, um trotz häufiger Beschleunigungen eine einwandfreie Wiederholgenauigkeit bieten zu können. Eine extrem hohe Steifigkeit in alle Richtungen wird sichergestellt durch verstärkte Ausgangslager mit Ritzeln, die in der Ausgangswelle integriert sind. Dieses einzigartige Konzept von REDEX ANDANTEX bietet eine Torsionssteifigkeit, die zu den besten auf dem Markt zählt; vor allem aber bietet es außergewöhnliche Steifigkeit entlang aller Ebenen (radial und axial). Dies ermöglicht oftmals eine zweifache Beschleunigung oder eine Verdoppelung des Gewichts im Vergleich zu anderen Lösungen.
Dieses exklusive Design kombiniert verstärkte Abtriebslager mit einem in der Abtriebswelle integrierten Ritzel gleichen Durchmessers wie die Abtriebswelle und mit gehärteten und geschliffenen Flanken. Der Flankendurchmesser wird optimiert, um das beste Verhältnis zwischen dem zu übertragenden Drehmoment und der Steifigkeit des Antriebsritzels sicherzustellen. Diese Lageranordnung wurde dafür entworfen, das Ritzel möglichst nah am Punkt der angreifenden Kraft zu stützen, nur getrennt durch die Dicke der Kontermutter. Diese besondere Konstruktion sorgt für eine erhebliche Reduzierung der radialen Ablenkung, die die Ursache von 60% der allgemeinen Verformungen ist und bei anderen Systemen nur in den seltensten Fällen zufriedenstellend gelöst wird.
Andantex USA ist der Lieferant für lineare Achsen und Drehachsen sowie für Getriebe, Zahnstangen und Ritzel. Alle Achsen sind mit ANDANTEX-Equipment ausgestattet, weshalb die Betriebseigenschaften der gesamten mechanischen Maschine einheitlich sind.
Der Zylinder der Drehachse treibt das Werkzeug an, auf dem die Carbonfaser platziert wird. Das Werkzeug ist in der Regel aus Invar hergestellt, einem Stahl mit sehr geringer thermischer Ausdehnung. Dies ist wichtig, denn sobald das Bauteil fertig gestellt ist, wird der ganze Aufbau in einem Autoklaven gebacken, um sicher zu stellen, dass die imprägnierte Carbonfaser in ihre endgültige Form aushärten wird. Danach wird das Werkzeug entfernt und das verbleibende Bauteil besteht komplett aus Carbonfaser. 4 KRP-Planetengetriebe, Größe 6, ermöglichen eine exakte Rotation.
Max. Rotationsgeschwindigkeit: 81 U/min
Nenndrehzahl: 25 U/min
Max. Drehmoment : 6600 Nm
Konfiguration: (2) Doppelantriebe/Achse
Die X-Achse besteht aus vier KRP-Planetengetrieben, Größe 6. Dies sind die Getriebe mit den größten Abmessungen in der Produktreihe REDEX ANDANTEX. Sie greifen über zwei 35 m große Gehäuse ineinander.
Lineare Geschwindigkeit = 51 m/min (2000 In/min)
Masse = 160 Tonnen (175 Tonnen US)
Beschleunigung = 0,2 g
Konfiguration: (2) Doppelantriebe/ Achse
Die Y-Achse ist mit zwei SRP-Planetengetrieben in einer TwinDRIVE Konfiguration ausgerüstet.
Sie sind in einem 5,5 m-Gehäuse montiert.
Lineare Geschwindigkeit = 53 m/min (2450 In/min)
Masse = 14,3 Tonnen (15,7 Tonnen US)
Beschleunigung = 0,2 g
Konfiguration: (1) TwinDRIVE/Achse
Für die sekundäre Geberrückführung auf der X- und Y-Achse nutzt Electroimpact auch das PDP- oder Split-Antriebsritzel von Andantex, um den Encoder direkt vom Gehäuse aus spielfrei antreiben zu können. Diese kostengünstige Lösung ist die erste Generation der "vorgespannten Doppelritzel" für hochpräzise Rack- und Antriebsritzel-Anwendungen.
Das PDP besteht aus zwei geschliffenen WMH-Ritzeln, die jeweils halb so breit sind wie das Gehäuse. Durch ein patentiertes Vorspannsystem sind sie miteinander verbunden, um ein Flankenspiel von Rack und Antriebsritzel eliminieren zu können. (** PDP Bild **) Das innovative PDP-Konzept bietet eine Geberrückführung direkt aus dem Rack sowie eine hohe Positionier-und Wiederholgenauigkeit bei sehr wettbewerbsfähigen Preisen.
- X-Achse Mod. 10, Umfang = 500 mm
- Y-Achse Mod. 5, Umfang = 250 mm
Schließlich lieferte Andantex Electroimpact die Module 10 & 5 spiralförmig, mit gehärtetem und geschliffenem Gehäuse für die X-und Y-Achse, zusammen mit Schmierstirnrädern aus Polyurethan für eine automatische Schmierung der Racks.
Die Gehäuse werden in 1- (oder 2-) Meter-Abschnitten geliefert und konstruiert und können an den Enden miteinander verbunden werden bis hin zur erforderlichen Achslänge. Andantex kann alle mechanischen Komponenten liefern vom Servomotor bis hin zur Achse.
»Die Bestückungspräzision entspricht der Präzision des Schneidevorgangs (+ / - 0,050) bei maximaler Geschwindigkeit. Die Achsen, angetrieben durch die Redex Andantex Reduzierstücke, müssen genauer sein als dieser Wert, da sie alle zusammenarbeiten, um eine komplexe Form zu bilden. Die Präzision von X-Achse, Y-und Z-Achse beträgt 1 / 10 der Präzision der Bauteilebestückung oder + / - 0,005 (0,0125 mm)», erklärt Dave REGIEC, Projektleiter bei ANDANTEX.
Fordern Sie weitere Informationen an…