www.konstruktion-industrie.com
11
'19
Written on Modified on
Wie Sandvik die erste unzerstörbare Gitarre der Welt aus dem 3D-Drucker herstellte
Seit vielen Jahrzehnten lieben es Rockstars, ihre Gitarren auf der Bühne zu zerstören. Und kaum jemand zeigt dabei mehr Einsatz als der schwedische Gitarrenvirtuose Yngwie Malmsteen.
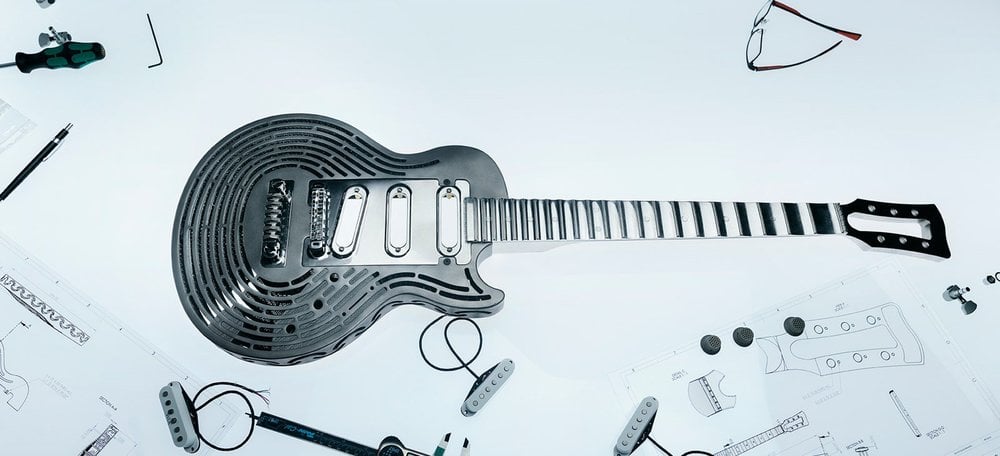
Sandvik holte Experten aus dem ganzen Unternehmen an einen Tisch, um zu beweisen, dass man mit nachhaltigen, innovativen Verfahren etwas schaffen kann, das gleichzeitig hochpräzise und unglaublich stabil ist.
„Da wir keine Produkte für Verbraucher herstellen, wissen die meisten Menschen nicht, wie weit vorne unsere Methoden wirklich sind“, sagt Klas Forsström, Präsident von Sandvik Machining Solutions.„Mit dem Bau einer unzerstörbaren Gitarre für einen anspruchsvollen Musiker wie Malmsteen stellen wir all die Fähigkeiten unter Beweis, die wir für die komplexen Herausforderungen in der Fertigung mitbringen.“
Die Ingenieure von Sandvik arbeiteten mit dem renommierten Gitarrentechniker Andy Holt von Drewman Guitars zusammen, um Malmsteens anspruchsvollem musikalischen Standard und seiner blitzschnellen Spielweise gerecht zu werden.
Die erste unzerstörbare Gitarre der Welt
Henrik Loikkanen, Zerspanungsprozessentwickler bei Sandvik Coromant, spielte schon als Jugendlicher Gitarre und war schon damals Fan von Yngwie Malmsteen. Um zu verstehen, was passiert, wenn Malmsteen ein Instrument zerstört, machte sich Loikkanen deshalb bei YouTube schlau.
„Wir mussten eine Gitarre entwickeln, die gut klingt – und die jedem Versuch standhält, sie zu zerstören“, erklärt Loikkanen.„Die technische Herausforderung war die Verbindung zwischen Hals und Korpus, die meist als erstes bricht.“
Die Lösung war denkbar einfach: Die Ingenieure von Sandvik verzichteten auf diese Verbindung. Stattdessen wurden Hals und Griffbrett auf einer einzigen Maschine aus recyceltem Edelstahl gefräst – eine Gitarrenbauweise, die noch nie zuvor ausprobiert wurde. Sowohl der Hals als auch das Griffbrett laufen in einem rechteckigen Mittelstück aus, das weit in den Korpus der Gitarre hineinreicht.
Daten auf dem neuesten Stand
Lange, schlanke Komponenten wie das Griffbrett und der Hals sind besonders anfällig für Verzug im Zerspanungsprozess. Dank zukunftsweisender Software konnte Sandvik Coromant den Fräsvorgang digital simulieren, bevor der erste Schnitt gemacht wurde. Dies ermöglichte eine optimale Werkzeugwahl, sparte Fertigungszeit und sorgte für effiziente Prozesse.
„Präzision war entscheidend“, erklärt Henrik Laikkanen, Zerspanungsprozessentwickler bei Sandvik Coromant.„Unsere Software basiert auf jahrelanger Erfahrung und liefert Empfehlungen zum Werkzeug und zu den Schnittdaten, mit deren Hilfe wir den Gitarrenhals an einigen Stellen bis auf eine Dicke von nur einem Millimeter fräsen konnten.“
Korpus Schicht für Schicht im 3D-Drucker hergestellt
Währenddessen wurde eine weitere Herausforderung angegangen: die Herstellung des Gitarrenkorpus, eines extrem komplexen Bauteils, das äußerst stabil und gleichzeitig leicht sein muss.
Sandvik nutzte seine weltweit führende Kompetenz bei Metallpulver und der additiven Fertigung: Die Ingenieure entschieden sich, den Korpus im 3D-Druck herzustellen. Dazu wurde feinstes Titanpulver von einem Laser zu übereinander liegenden Schichten verschmolzen. Diese Schichten, jede dünner als ein menschliches Haar, bildeten schließlich den Korpus der Gitarre.
„Mithilfe der additiven Fertigung können wir leichtere, festere und flexiblere Bauteile mit inneren Strukturen herstellen, die unmöglich auf herkömmliche Weise gefräst werden könnten“, erläutert Amelie Norrby, Ingenieurin für additive Fertigung, die am Gitarrenprojekt beteiligt war. „Und sie ist nachhaltiger, weil wir nur das Material verwenden, das für die Komponente benötigt wird und so jeglichen Abfall vermeiden.“
Die Welt der Werkstoffe
Tomas Forsman, Forschungs- und Entwicklungsspezialist bei Sandvik, erkannte, dass für die Gitarre eine spezielle Struktur notwendig ist, die fest, steif und leicht zugleich ist. Sein Vorschlag: eine isotrope Leichtbaustruktur (Isotropic Lightweight Structure, ILS) – die stabilste Struktur im Verhältnis zum Gewicht, die jemals entwickelt wurde.
„Sie sieht eigentlich wie jede andere Rahmenstruktur aus“, so Forsman, „aber sie ist steifer und leichter als alles, was vorher entwickelt wurde.“
Forsman wusste auch genau, aus welchem Werkstoff die ILS hergestellt werden sollte: Hyper-Duplexstahl, eine Sorte, die nur Sandvik produziert. Er wollte die Hyper-Duplex-ILS zwischen dem Hals und dem Griffbrett in Sandwichbauweise unterbringen.
Allerdings musste das Griffbrett absolut verwindungsfrei bleiben – ein Problem, das beim Verschweißen langer, dünner Komponenten häufig auftritt. Darum wurde der Schweißprozess durch Untersuchungen und Tests so weit verfeinert, dass die ILS am Ende erfolgreich integriert werden konnte.
Forsman ist der Meinung, dass die umfassende Zusammenarbeit bei dem Gitarrenprojekt eines klar zeigt: Mit dem umfangreichen Wissen und der Erfahrung von Sandvik lassen sich einzigartige Herausforderungen meistern – selbst bei engen Zeitvorgaben.
„Diese Art der Zusammenarbeit ist der Schlüssel zur Zukunft“, sagt Forsman. „Die Anforderungen unserer Auftraggeber werden immer komplexer. Wir müssen unser geballtes Know-how einbringen, um gemeinsam mit Partnern und Kunden neue Wege zu finden, um diesen Anforderungen gerecht zu werden.“
Live, in Concert
Als die Gitarre fertig war, übergab Sandvik sie an Malmsteen.Dieser spielte damit in einem Club in Florida zunächst einige Songs und begann dann, die Gitarre gegen Verstärker, Bühnenaufbauten und auf den Fußboden zu schlagen, um sie zu zerstören.
„Diese Gitarre ist ein Biest!“, sagte Malmsteen, als er seine Bemühungen aufgegeben hatte, sie zu zertrümmern. „Die Jungs von Sandvik sind offensichtlich ganz weit vorne bei dem, was sie tun. Sie haben hart gearbeitet und ihre Hausaufgaben gemacht. Das passt zu mir. Das Ergebnis ist einfach großartig. Ich habe wirklich alles gegeben, aber sie ist nicht kaputt zu kriegen.“
www.sandvik.com
Fordern Sie weitere Informationen an…