www.konstruktion-industrie.com
28
'12
Written on Modified on
Einst das schwächste Glied – jetzt Superstar der Zerspantechnik
Warum der neue Spindelanschluss die Spanabfuhr maximiert
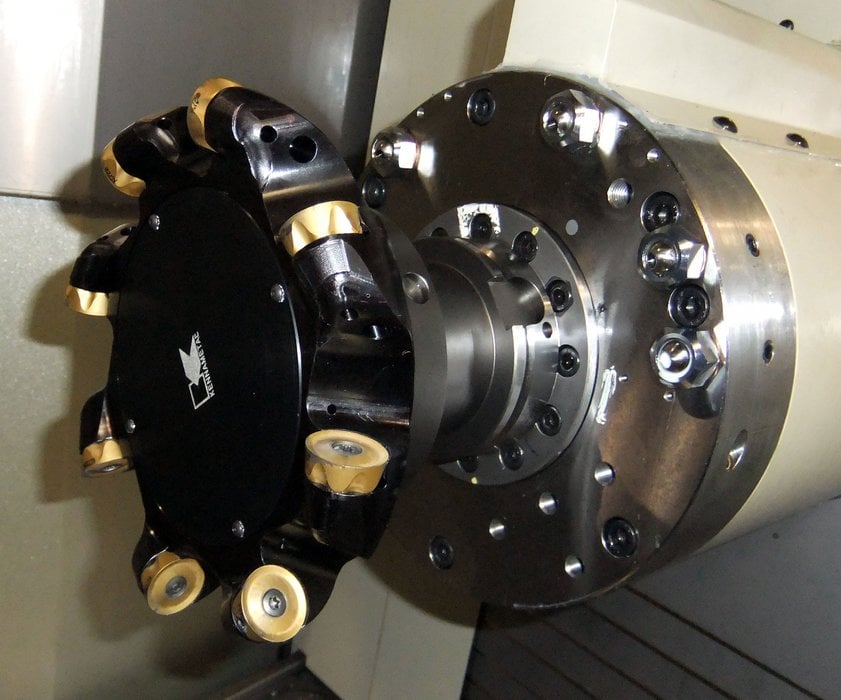
Mark Huston, Vice President, Global Engineered Solutions
Doug Ewald, Director, Global Product Management, Tooling Systems
Ruy de Frota de Souza, Manager, Global Tooling Systems, Product Engineering
Kennametal Inc., Latrobe, PA
Zähe Materialien wie Titan zu zerspanen ist in sich schon eine Herausforderung. Harte Legierungen unter dem zusätzlichen Druck verbesserter Produktionseffizienz zu zerspanen bedeutet die Spanabfuhr bei niedrigen Schnittgeschwindigkeiten und beträchtlichen Schneidkräften zu maximieren. Die Hersteller von Werkzeugmaschinen begegnen dem mit speziellen Fräs- und Drehzentren, die eine verbesserte Steifigkeit und Dämpfung der Spindeln und ziemlich große Maschinengestelle aufweisen; all dies, um unerwünschte Vibrationen zu minimieren, die die Qualität des Teils und die Standzeit des Werkzeugs herabsetzen würden. Obgleich derartige Fortschritte zu einer größeren Produktivität beigetragen haben, blieb der schwächste Punkt der Spindelanschluss selbst.
In den meisten Fällen bestimmt die Verbindung Werkzeug/Spindel die Größe des Zerspanvolumens (metal removal rate). Dies deswegen, weil diese Schnittstelle hohen Lasten standhalten und dabei doch ihre Steifigkeit beibehalten muss, so lange bis die Werkzeugablenkung zu hoch ist oder Rattern einsetzt. Angesichts der derzeitigen Fortschritte bei Schneidwerkzeugen und Bearbeitungszentren sollte unbedingt ein Spindelanschluss, der die beste Nutzung der zur Verfügung stehenden Leistung ermöglicht, bereits bei der Planung der Produktion in Betracht gezogen werden.
In den vergangenen Jahrzehnten wurden mehrere Bauarten von Spindelanschlüssen entwickelt und vervollkommnet. Wegen seines günstigen Kosten-Nutzen-Verhältnisses gewann der Kegel 7/24 nach ISO seine Vorrangstellung auf dem Markt. Zwar war er in vielen Anwendungen der Anschluss der Wahl, aber Grenzen von Genauigkeit und Schnittgeschwindigkeit setzen seiner weiteren Verbreitung Grenzen.
Die Einführung der Plananlage war ein großer Fortschritt gegenüber 7/24-Kegel. Die Kombination von Plananlage und massivem 7/24-Kegel liefert eine höhere Genauigkeit in der Z-Achse, hat aber auch ihre Nachteile, nämlich Verlust an Steifigkeit bei höheren Geschwindigkeit oder bei seitlicher Belastung. Die meisten Werkzeuge auf dem Markt sind massiv und die Spindeln haben verhältnismäßig niedrige Spannkräfte. Die Steifigkeit der Verbindung ist begrenzt, da die radiale Pressung auf ein Minimum beschränkt werden muss. Die zum Erreichen eines konsistenten Flächenkontakts erforderlichen Toleranzen sind daher sehr eng, was hohe Fertigungskosten zur Folge hat.
Im Jahr 1985 initiierten Kennametal und Krupp WIDIA ein gemeinsames Programm zur Entwicklung eines universellen Schnellwechselsystems, inzwischen bekannt als KM™ und kürzlich als ISO 26622 genormt. In den frühen 90er Jahren wurde das System HSK nach und nach auf Maschinen in Europa verwendet, das dann die DIN 69893 und später die ISO 12164 wurde.
Das Werkzeug-Schnellwechselsystem KM™ besteht aus zwei Grundkomponenten, der Spanneinheit und dem Schneidkopf. Die Spanneinheit sitzt auf dem Werkzeug (ein Revolver oder ein Werkzeugblock für stationäre Anwendungen und eine rotierende Spindel für rotierende Anwendungen) und ist die Aufnahme für die austauschbare Schneideinheit bzw. den austauschbaren Werkzeughalter. Wird ein Werkzeugwechsel notwendig, löst der Bediener lediglich die Verriegelung, tauscht die Schneideinheit aus und verriegelt sie in ihrer Position. Stillstandszeiten reduzieren sich auf Sekunden.
KM4X™ von Kennametal ist die Nachfolgegeneration des Systems KM. Manche Systeme sind wohl in der Lage, ein beträchtliches Drehmoment zu übertragen, jedoch erzeugen Schnittkräfte Biegemomente, die die Aufnahmefähigkeit der Schnittstelle überschreiten noch bevor die Grenze hinsichtlich des Drehmoments erreicht ist. In der Kombination von hoher Spannkraft und optimiertem Festsitz liefert KM4X eine robuste Verbindung, extrem hohe Steifigkeit und Biegefestigkeit mit dem Ergebnis von wesentlich verbesserter Leistung bei der Bearbeitung hochfester Legierungen und anderer Materialien durch Erhörung des Zerspanvolumens und letztlich mit dem Ergebnis auch einer erhöhten Zahl fertiger Teile pro Tag.
3-fach verbesserte Biegefestigkeit
Die Spindelverbindung muss ein Drehmoment übertragen können und eine Biegefestigkeit aufweisen, die mit der Spezifikation der Werkzeugmaschine und den Anforderungen höherer Produktivität in Einklang stehen. Dies wird bei Schaftfräser-Anwendungen deutlich, wo die Projektionslängen typischerweise größer sind und die Biegefestigkeit den einschränkenden Faktor darstellt. Ein Beispiel: Ein Wendeschneidplatten-Fräser mit spiralförmiger Schneide, 250 mm Projektion von der Spindelfläche und 80 mm Durchmesser bewirkt ein Biegemoment von 4620 Nm und ein Drehmoment von weniger als 900 Nm bei einem Materialabtrag von 360 cm3/min im Falle von Ti6Al4V bei radialer Schnitttiefe = 12,7 mm und axialer Schnitttiefe = 63,5 mm.
Die kritischsten Parameter einer Spindelschnittstelle mit Kegel-Plananlage-Kontakt sind die Spannkraft und das radiale Übermaß. Die Maximierung der Spannkraft und eine angemessene Wahl der Werte für das Übermaß können die Steifigkeit der Schnittstelle weiter erhöhen.
Durch einen Drei-Plananlage-Kontakt (voderer Bereich des Kegels und der hintere Bereich des Kegels) zur verbesserten Stabilität und durch eine Optimierung der Spannkraftverteilung und des
Übermaßes ergibt die Technologie von KM4X eine dreifach höhere Biegefestigkeit gegenüber anderen Werkzeugsystemen.
Dies bedeutet:
-Die Fertigung kann mit KM4X ausgestattete Hochleistungs-Werkzeugmaschinen mit erhöhter Geschwindigkeit und Vorschüben in schwierigen spanabhebenden Einsätzen wirksam einsetzen und gewinnt so das volle Produktivitätspotential der Werkzeugmaschine.
-Oft wird eine kleinere KM4X-Schnittstelle wie zum Beispiel die KM4X100 die selbe oder sogar eine bessere Schneidleistung im Vergleich zur größeren Schnittstelle erbringen.
-KM4X-Systeme können in Multitasking, Dreh- und Bearbeitungszentren wie auch in Palettentransfer-Maschinen in manueller, halbautomatischer oder vollautomatischer Betriebsart eingesetzt werden.
KM4X kann auf Grund der Konstruktion einen weiten Einsatzbereich abdecken, von niedriger Geschwindigkeit bei hohem Drehmoment bis zu hoher Geschwindigkeit bei niedrigem Drehmoment; so holen Hersteller das absolute Maximum aus ihrer Fertigungsausrüstung heraus.
Fräsen, Bohren und Drehen einer breiten Palette von Materialien wurde nun wirklich produktiver!
Regeln und Empfehlungen sind naturgemäß allgemein gehalten. Um eine spezifische Beratung zur Bearbeitung von Titan und weitere Informationen über KM4X zu erhalten, nehme man Verbindung zu Kennametal auf oder besuche www.kennametal.com.
KM4X_with_cutter.jpeg: Durch die Kombination von hoher Klemmkraft und optimiertem Übermaß stellt KM4X eine robuste Schnittstelle dar, bei extrem hoher Steifigkeit und Biegebelastbarkeit mit dem Ergebnis wesentlich gesteigerter Leistung bei der Bearbeitung von hochfesten Legierungen und anderen Materialien; sie bietet extrem hohen Materialabtrag und somit eine gesteigerte tägliche Fertigungsrate.
KM4X_8.jpeg: Das System der KM4X-Spindelschnittstelle von Kennametal weist eine hoch belastbare Anwendungsbreite auf, mit der in der Kombination hohe Geschwindigkeit/niedriges Drehmoment oder niedrige Geschwindigkeit/hohes Drehmoment gearbeitet werden kann. Ohne KM4X würden Spiral-Fräswerkzeuge wie dieses die Grenzen des zulässigen Biegemomentes lange vor Erreichen des maximal zulässigen Drehmomentes erreichen.
KM4X_9.jpeg: Kegel-Plananlage und Klemmkraft in Kombination ergeben verbesserten Übermaßsitz und dreifache Biegesteifigkeit gegenüber anderen Systemen. Werkzeugwechsel geschieht schnell und leicht und minimiert so die Stillstandszeit.
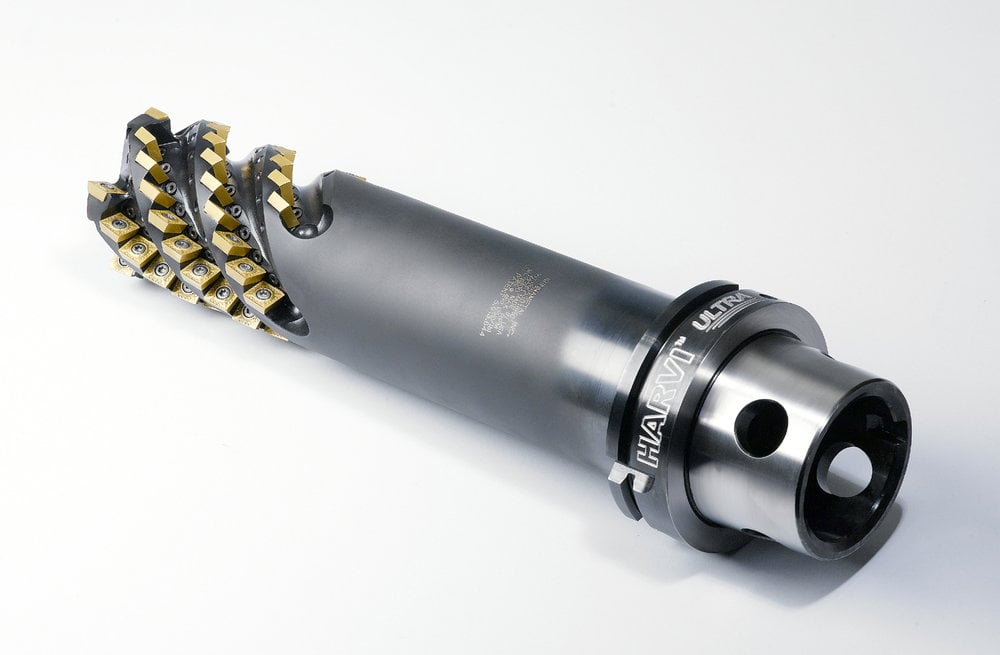
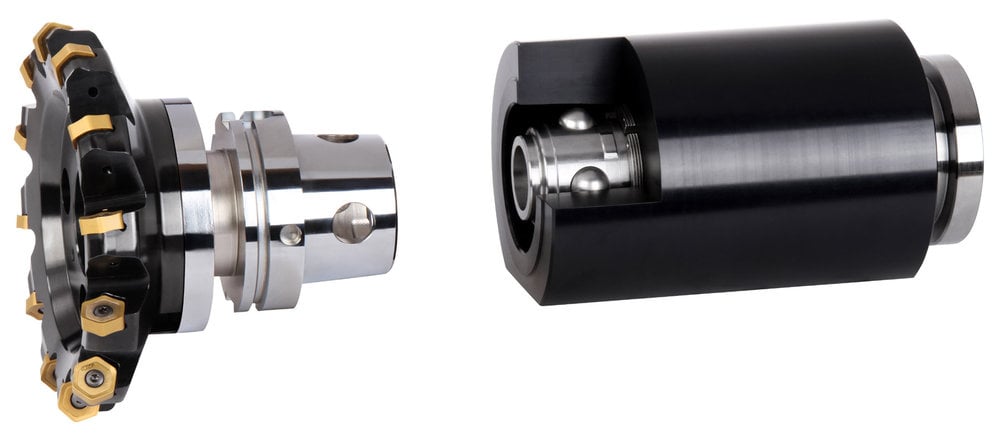
Fordern Sie weitere Informationen an…