www.konstruktion-industrie.com
17
'20
Written on Modified on
Verputzroboter in der Bandagenfertigung von Bomag
Schweißnähte perfekt in Form gebracht.
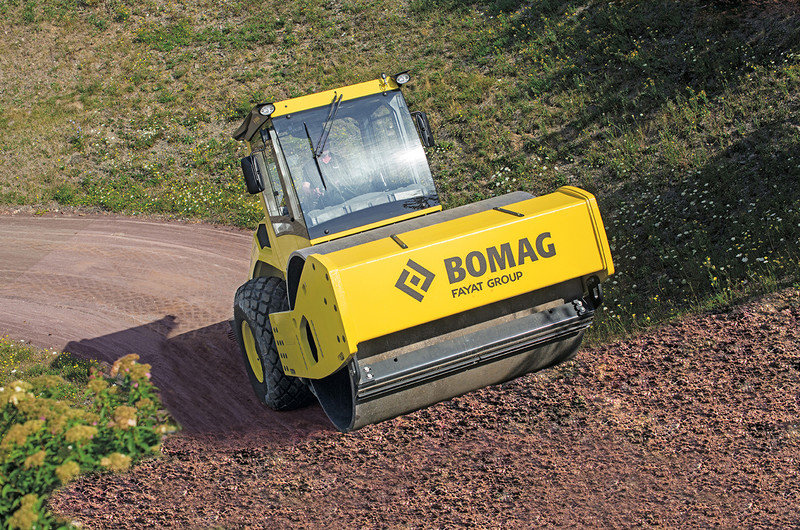
Bei der Fertigung der Bandagen für Walzenzüge setzt Bomag neueste Tech-nik ein. Viele Arbeitsschritte übernehmen Roboter – neuerdings auch das Verputzen der Schweißnähte. Das Ergebnis ist eine perfekt gerundete, tonnenschwere Bandage. Das schafft beste Voraussetzungen für glatte Pisten im Straßenbau.
Bis zu zwölf Tonnen wiegen die Bandagen, mit denen die mobilen Maschinen von Bomag den Untergrund für den Straßenbau verdichten und dabei durch Vibration unterstützt werden. In diesem anspruchsvollen Bereich der Baumaschinentechnik ist das Unternehmen mit Hauptsitz in Boppard am Rhein Weltmarktführer und hat 2013 ein neues Werk für die Bandagenfertigung der Walzenzüge in Betrieb genommen.
Hier werden die bis zu 60 mm starken Mantelbleche – die teilweise aus extrem verschleißfesten Hardox-Stählen bestehen – zunächst gerundet, wobei Biegekräfte von bis zu 6.000 Tonnen erforderlich sind. Dann folgt das vollständig automatisierte Schweißen der Längsnaht sowie der Tellerscheiben, d.h. der Seitenteile der Bandagen. Anschließend muss die Längsnaht auf der Bandage mit hoher Präzision verputzt werden. Denn jede noch so geringe Unrundheit würde die Qualität des Planums – das ist der Fachbegriff für den Unterbau der Asphaltschicht – beeinträchtigen.
Gesucht: Alternative zum Längsnahtfräsen
Ursprünglich übernahm eine Längsnahtfräsmaschine diese Aufgabe. Sie fräste die Überstände der Schweißnaht in einer linearen Bewegung ab und verursachte dabei sowohl Lärm als auch große Staubentwicklung. Außerdem entsprach die Genauigkeit des Prozesses nicht den Ansprüchen von Bomag.
Deshalb suchten die Verantwortlichen von Bomag nach einer Alternative zum Fräsen und schauten sich dabei auch in der Robotik um. Denn viele Prozesse der Bandagenfertigung – bis hin zum Materialtransport per Schwerlast-FTS – sind bereits automatisiert.
Der Kontakt zu dem Unternehmen, das die Lösung schließlich entwickelte und umsetzte, kam eher zufällig zustande: Harald Aßmann, Teamleiter der Bandagenfabrik, folgte der Einladung zu einer Yaskawa-Hausmesse und informierte sich dort über die Möglichkeiten des robotergestützten Schleifens. Die Informationen waren überzeugend: „Wir haben mehrere Projektbeispiele von Schleifrobotern kennengelernt. Das hat uns gezeigt: Yaskawa ist der richtige Partner.“
Erster Schritt: Vermessen der Schweißnaht
Nach intensiver Projektarbeit installierte Yaskawa in der Bomag-Bandagenfertigung eine komplett eingehauste Anlage, in der die Bandage per Kran auf einer ebenfalls von Yaskawa gefertigten drehbaren Vorrichtung abgelegt wird, wobei sich die Schweißnaht in „12:00 Uhr-Position“ befinden muss.
Der Bediener startet das Programm und schließt die Einhausung. In der Zwischenzeit hat der Roboter, ein großer, sechsachsiger MOTOMAN MH180, bereits ein Lasermessgerät aus dem Werkzeugwechsler entnommen und vermisst im ersten Schritt die Schweißnaht sehr genau. Dabei verfährt der Roboter nicht linear, sondern in einer Pendelbewegung entlang der Kontur der Bandage, um die Schweißnaht dreidimensional zu erfassen.
Zweiter und dritter Schritt: Schleifen von Längsnaht und Seitenscheibe
Die Daten, die das Messgerät generiert, bilden die Basis für den nachfolgenden Bearbeitungsschritt. Der Roboter wechselt auf einen Bandschleifer und fährt damit zehn- bis zwölfmal über die Schweißnaht. Die Stromaufnahme des Roboters dient dabei als Parameter für die Bearbeitungsqualität: Wenn genug Material abgetragen ist, muss das Schleifwerkzeug weniger Druck aufbringen und der Bearbeitungsvorgang kann beendet werden. Auch am Ansatz, d.h. an den Kanten der Bandagen, wird Material abgetragen.
Auch beim Schleifen vollzieht der MOTOMAN MH180 eine nichtlineare Bewegung, um die komplette Kontur der Schweißnaht zu bearbeiten. Zusätzlich dreht sich auch die Vorrichtung. Harald Aßmann: „So sparen wir Platz: Der Roboter hat zwar eine sehr große Reichweite, kann aber dennoch bei großen Bandagen nicht die gesamte Länge abdecken.“
Die Drehbewegung wird auch für den dritten Arbeitsschritt benötigt. Hier legt der kräftige Roboter den Bandschleifer ab und verputzt mit einem Orbitalschleifer die Schweißnaht, mit der die Seitenscheiben und der Außenmantel der Bandage verbunden sind. Das Ergebnis des robotergestützten Verputzens in drei Schritten ist eine tadellos ebene Schweißnaht, die sich perfekt in die Rundung der Bandage einfügt, und eine saubere Verbindung von Seitenscheibe und Bandage.
Zu den Besonderheiten des „Verputzroboters“, wie er bei Bomag genannt wird, gehört die durch einen Deckel geschützte Werkzeugablage, die nur beim Wechseln selbsttätig öffnet. So bleiben die Werkzeuge sauber. Den MOTOMAN MH180 selbst schützt eine Ummantelung vor Staub und Funkenflug – eine reine Vorsichtsmaßnahme, denn die leistungsfähige Absaugung zieht nahezu alle Funken ab.
Verputzen ohne Zeitverlust – mit hoher Flexibilität
Vorteilhaft aus Sicht der Produktivität: Der Arbeitsschritt findet ohne Zeitverlust statt. Harald Aßmann: „Das Verputzen erfolgt parallel zum Einbringen der Bohrungen in die Seitenscheiben.“ Und flexibel ist die Anlage, die seit rund sechs Monaten läuft, auch. Dennis Anton, für die Programmierung des Verputzroboters zuständig: „Wir haben inzwischen Programme für knapp 40 Bandagentypen mit Durchmessern bis zu über zwei Metern und verschiedensten Längen geschrieben.“
Mit dem Projektverlauf sind die Bomag-Verantwortlichen ebenfalls zufrieden. Kleine „Sonderwünsche“ wurden noch vor Ort berücksichtigt. So hat Dennis Anton angeregt, dass die vorhandene Pneumatikleitung im Roboter dazu benutzt wird, um im letzten Arbeitsgang Schweißperlen und Schleifrückstände aus der Innenseite der Bandage auszublasen.
Alles in allem ist der neue Roboter aus Sicht von Bomag ein beispielhaftes Automatisierungsprojekt. Harald Aßmann abschließend: „Wir haben die Effektivität gesteigert, weil die Kollegen nicht mehr manuell nachschleifen und verputzen müssen. Das reduziert auch die körperliche Belastung der Mitarbeiter, die sich in dieser Zeit anspruchsvolleren Aufgaben widmen können.“ Und in der gesamten Bandagenfabrik wurden die Lärm- und Staubemissionen gesenkt.
www.yaskawa.com
Fordern Sie weitere Informationen an…