www.konstruktion-industrie.com
07
'16
Written on Modified on
Magnetfeld statt Vorschubwalzen
Mit Antriebsreglern von Kollmorgen entwickelt tecodrive ein revolutionäres Verfahren für den Materialvorschub „fleXfeed“ hat die tecodrive GmbH aus Garbsen ihre Erfindung getauft – und betritt damit auf revolutionäre Weise Neuland im Materialvorschub der Metallverarbeitung. „fleXfeed“ arbeitet dank eines ausgeklügelten Magnetfeldes vollkommen berührungsfrei und ist deutlich schneller als herkömmliche Walzenvorschübe. Das junge Unternehmen nutzt für seine neue Lösung das Prinzip der linearen Direktantriebstechnik. Kollmorgen war eng in die Entwicklung als Partner für die Umsetzung der Antriebsregelung eingebunden. Die Servoumrichter S700 nehmen im kontaktfreien Vorschub eine Schlüsselrolle ein.
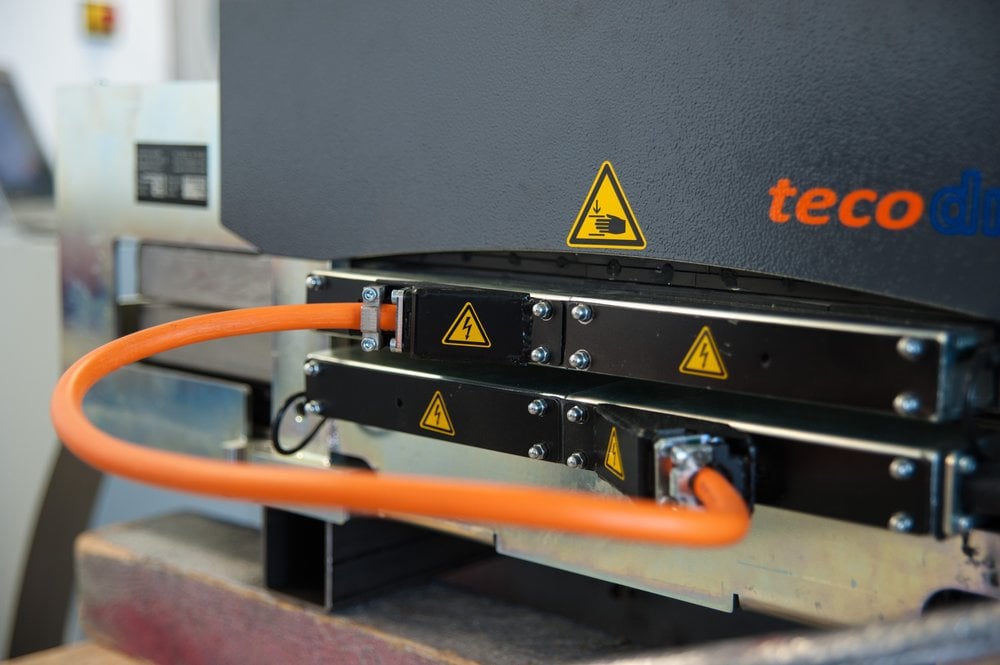
Weder Torsion noch ein Durchrutschen
Wer die Vorteile der elektromagnetischen Lösung vollständig erschließen will, wirft am besten einen kurzen Blick in die Arbeitsweise eines Walzenvorschubs. Dieser positioniert einen Blechstreifen von einem Coil kommend taktend in eine Bearbeitungsmaschine – zum Beispiel eine Anlage zum Tiefziehen oder Stanzen. Bei jedem Takt müssen die beiden Rollen schließen, Druck auf das Werkstück aufbauen, dieses kraftschlüssig transportieren und nach Abschluss wieder öffnen – also lüften. „Je höher die Geschwindigkeit ist, desto höher muss der Druck sein, damit das Material nicht durchrutscht“, erklärt Marthiens. Und genau hier liegt der Nachteil der Walzenvorschübe im Vergleich zur elektromagnetischen Umsetzung. Die Presskraft auf den Werkstoff lässt sich nicht ins Unendliche steigern, weil sich das Metall sonst verformt. Zudem steigt das Risiko, fein bearbeitete Oberflächen zu beschädigen. Bei TriluX hat dieser Effekt etwa dafür gesorgt, dass sich in die Aluminiumlamellen eine kaum sichtbare Torsion eingeschlichen hat. Diese sorgte nach der fertigen Montage aber regelmäßig dafür, dass sich der Lichtschein merkwürdig verformte.
Heute setzt der Leuchtenhersteller den „fleXfeed“ von tecodrive ein – mit erstaunlichen Ergebnissen. Das Unternehmen fährt jetzt mit doppelter Geschwindigkeit und kann die Leistungsfähigkeit der Blechbearbeitungsmaschinen endlich voll ausnutzen. „Unser Auftrag bestand am Anfang des Projektes darin, 400 Hübe in der Minute zu erreichen – was wir sehr einfach geschafft haben“, blickt Hans-Jörg Lindner, ebenfalls geschäftsführender Gesellschafter von tecodrive, zurück. „Wir erreichen bei bestehenden Prozessen in der Regel eine Steigerung mit Faktor zwei“, ergänzt Dr. Marthiens.
Woher kommt diese Leistung? Wie bei der linearen Direktantriebstechnik auch, nutzt der kontaktfreie Vorschub das Prinzip der magnetischen Anziehung beziehungsweise Abstoßung. Dafür sind in dem nur knapp ein Meter langen Gerät zwei Statoren gegenüberliegend angeordnet. Sie erzeugen im dazwischen liegenden Metallband eine magnetische Wanderwelle, die dank der dabei entstehenden Lorenz-Kraft für den Vorschub genutzt wird. Das Wirkprinzip lässt sich im „fleXfeed“ mit einem asynchronen Linearantrieb vergleichen, bei dem das Metallblech die Rolle des Kurzschlussläufers einnimmt. Dieses Detail bringt für die Regelungstechnik jedoch einige Herausforderungen mit sich, die letztlich auch den Kern des patentierten Verfahrens bilden.
Neues Regelverfahren entwickelt
Und genau an dieser Stelle nutzt tecodrive die Leistungsstärke der S700-Servoregler von Kollmorgen – vor allem was die Schnelligkeit und Programmierbarkeit betrifft. Die maximalen Freiheitsgrade braucht Dr.-Ing. Olaf Marthiens, um eine neue Regelungsart in den Servoumrichter zu implementieren, die abweicht von der feldorientierten Vectorreglung (FOC). „Ich musste ein Programm schreiben, mit der ich den Phasenwinkel des Stroms und die Amplitude verändern kann.“ Die Verwendung der FOC funktioniere in diesem speziellen Einsatzgebiet nicht, weil das sich ständig ändernde magnetische Verhalten des zu transportierenden Werkstoffes den Regelkreis instabil machen würde. Die FOC reagiere ganz empfindlich auf die so genannte Rotorkonstante - also das Verhältnis der Induktivität und dem elektrischen Widerstand des zu fördernden Bleches. In einem Standardasynchronmotor ist der Rotor mechanisch unverändert und die Rotorkonstante nur von der Temperatur abhängig. Selbst das kann einen Applikator zur Weißglut bringen beim Einsatz von Asynchronmotoren in hochdynamischen Regelanwendungen.
Die „fleXfeed“ Einheit ist hingegen genau dafür konzipiert, möglichst viele unterschiedliche Metallwerkstoffe in einer Bearbeitungsmaschine hochdynamisch und genau zu positionieren. Deshalb kommt es auch durch unterschiedliche Dicken, Breiten und unsichtbare Veränderungen des Materialgefüges zu immer wieder neuen Widerstands- und Induktivitätswerten – und damit veränderten Rotorkonstanten.
tecodrive hat dieses Problem gemeinsam mit Kollmorgen dahingehend gelöst, dass es in dieser Anwendung nur noch einen Strom- und Lageregler gibt. Es gibt keine feldorientierte Regelung mehr, weil der Servoumrichter S772 so programmiert ist, dass er das Feld fix vorgibt. „Hier steckt unser besonderes Know-how drin“, merkt Marthiens mit Begeisterung an. Für die Positionsbestimmung des Blechs greift tecodrive zu eigenentwickelten Messrädern als Rückführung. Bemerkenswert ist die Schnelligkeit des Regelkreises, weil tecodrive ohne Umweg über eine Steuerung oder den Feldbus direkt aus der tatsächlichen Lage des Blechs im Magnetfeld den nächsten Sollwert berechnet. „Wir brauchen die absolute Verzögerungsfreiheit, um selbst bei einer Taktzahl von 4000 Hüben pro Minute noch mit 10µm genau zu positionieren. Die Spitzenwerte sind mit eine Folge der hohen Rechenperformance der S700-Regler sowie der insgesamt sehr schlanken und übersichtlichen Programmierung. Marthiens freut sich noch heute über die enge Zusammenarbeit mit dem Kollmorgen-Vertriebsteam, das die Bedeutung dieser Erfindung sofort erkannte und auch den direkten Kontakt zu Georg Jaskowski, Softwareentwickler der S700-Reihe bei Kollmorgen herstellte.
Ungeahnte Produktivität beim Vorschub
tecodrive und Kollmorgen haben es geschafft, einen Vorschub zu konzipieren, der Kennzahlen erreicht, die mit Walzen niemals möglich wären - allein schon deshalb, weil sich die Massen gar nicht so schnell ausregeln lassen. Der Vorschub besitzt hingegen keine eigene Masse, weil er nur aus einem Magnetfeld besteht. Der Prozess reduzierte sich damit – einfach ausgedrückt – auf das masselose Ein- und Ausschalten des Stroms. Mit diesem genialen Prinzip sind noch weitere Vorteile in der Praxis verbunden. Das Schalten erfolgt geräuschlos und frei von mechanischen Belastungen. Dieser Aspekt steigert gerade im Hochleistungsbetrieb erheblich die Lebensdauer der Produktionsmittel, weil es keinen mechanischen Verschleiß in der Vorschubeinheit gibt.
Geringer Energieverbrauch
Und noch ein weiterer Punkt lässt aktuell auch Firmen im direkten und indirekten Automobilumfeld aufhorchen: Die Neuentwicklung braucht auch nur ein Bruchteil der Energie, die ein Walzenvorschub zur Versorgung nimmt. „Wir müssen zwar einen 35 kW Servoregler von Kollmorgen einsetzen, um den notwendigen Magnetisierungsstrom zu erreichen, die reine Wirkleistung beträgt aber nur 700 Watt“, erklärt Dr.-Ing. Olaf Marthiens. Für seinen Mitgeschäftsführer Hans-Jörg Lindner sind auch dieses Vorteile, die dafür sprechen, in der Materialzuführung gewohnte Wege zu verlassen. „Wir haben es bei TriluX geschafft, aus zwei Anlagen eine zu machen – und dieses bei gleicher Produktivität nur mit deutlich weniger Platzbedarf und Aufwand für die Werkzeuge.“ Ähnlich gute Erfahrungen habe es auch bei VW in Hannover Stöcken gegeben.
Bildtexte
Bild 1
Prinzipbild: Der kontaktfreie Vorschub beruht auf dem Prinzip magnetischer Anziehung und Abstoßung. Zwei Statoren erzeugen dafür im Metallband eine magnetische Wanderwelle. Bild: tecodrive
Die beiden Statoren erzeugen in der Vorschubeinheit ein kräftiges Magnetfeld, das wiederum von einem Kollmorgen Servoregler gesteuert wird.
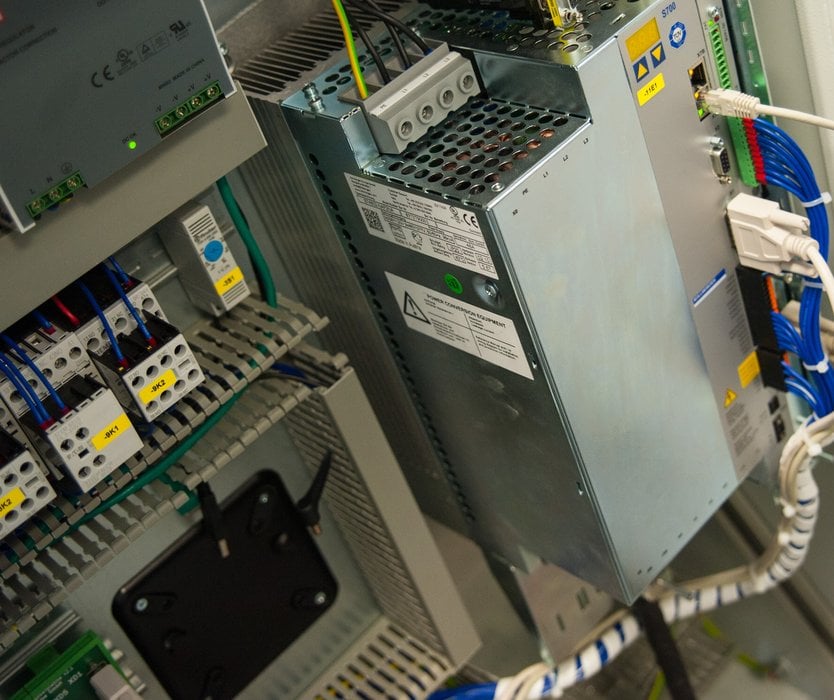
Kollmorgen-Servodrive-S772
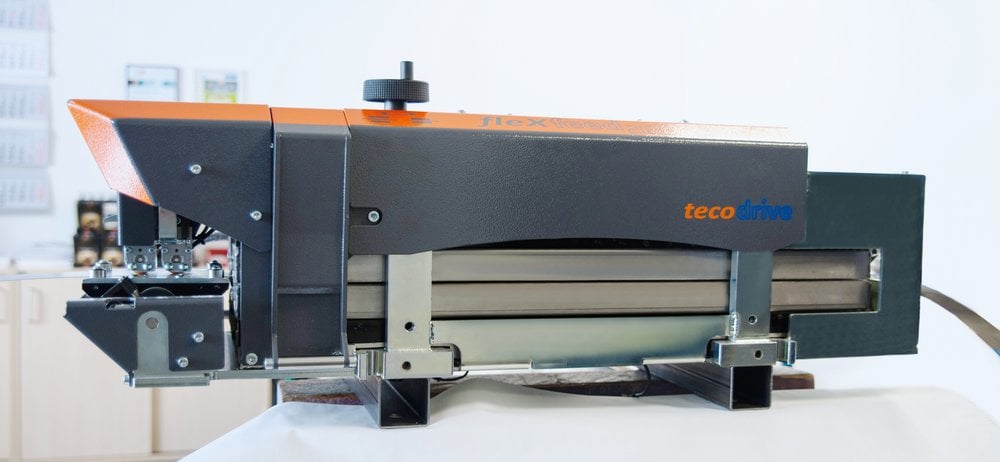
tecodrive-fleXfeed

Bild 6
Das findiger Trio von tecodrive in Hannover: Dr.-Ing. Olaf Marthiens, Hans-Jörg Lindner und Hannes, Mahler (vor rechts).
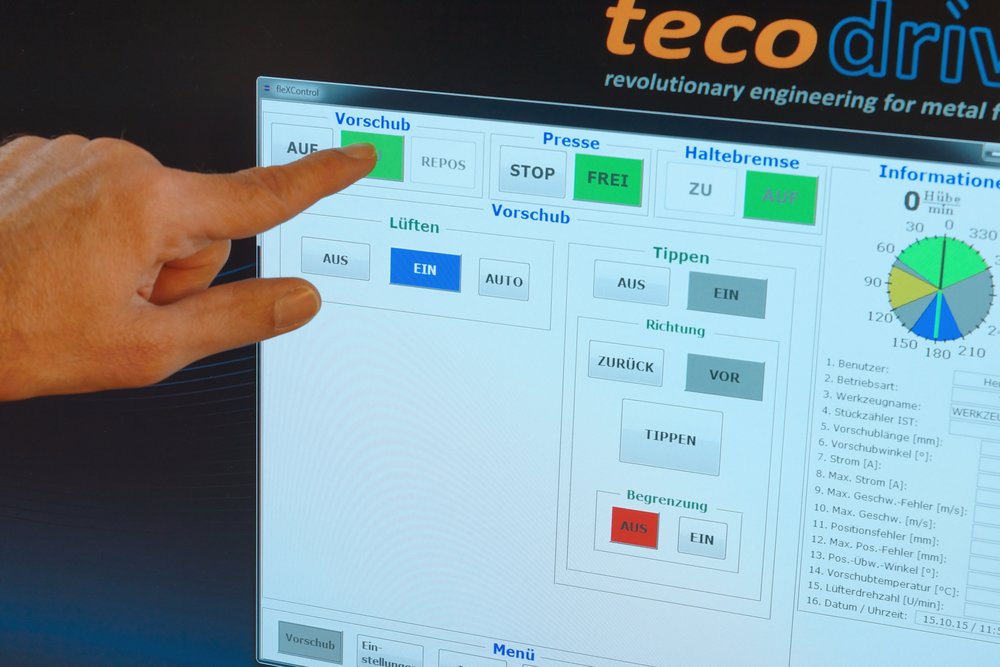
tecodrive
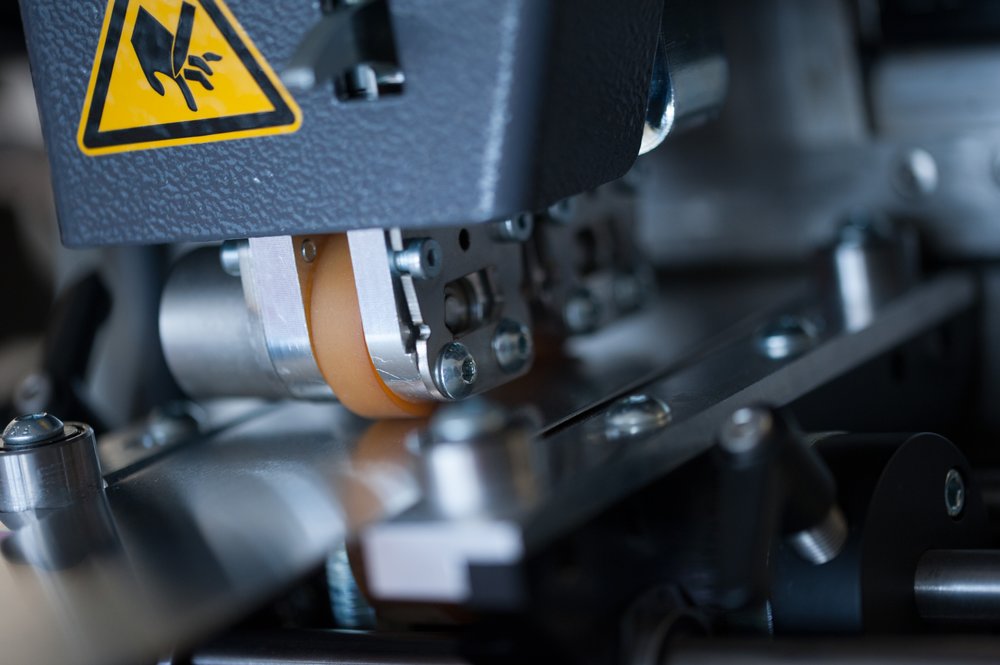
tecodrive-fleXfeed-Messrad
Keine zwei Meter lang: „fleXfeed“ bringt neues Tempo in die Produktzuführung der Metallverarbeitung.
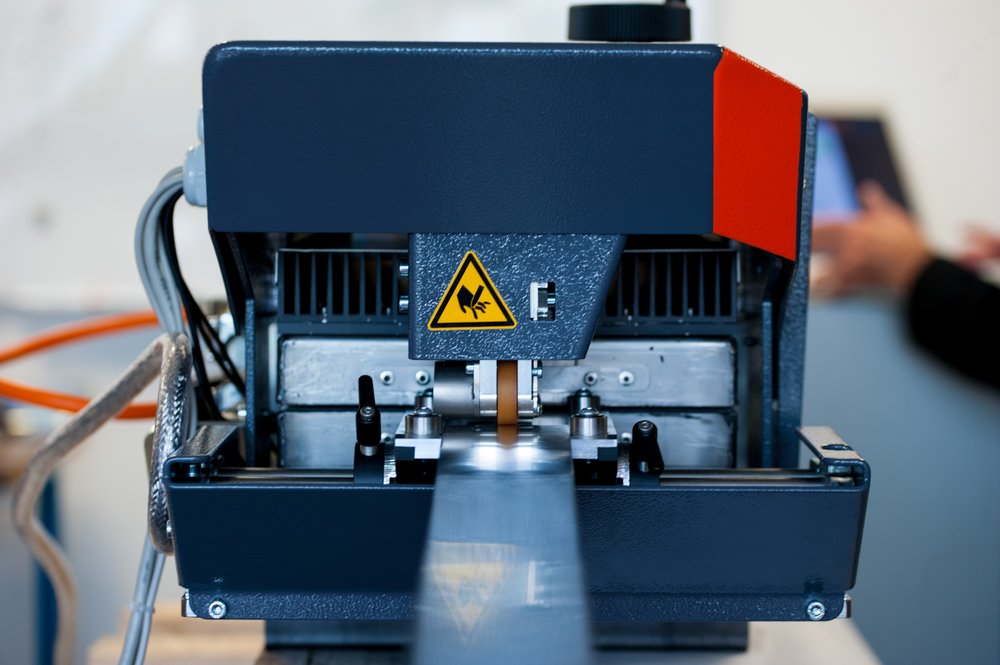
tecodrive-fleXfeed-Frontansicht.
Fordern Sie weitere Informationen an…