www.konstruktion-industrie.com
25
'17
Written on Modified on
Unidrive M700 maximiert in einem Kraftwerk die Leistung des Kühlturms und senkt gleichzeitig die Wartungskosten
In dem Kraftwerk Possum Point Power Station werden neuerdings Umrichter der Reihe Unidrive M700 von Control Techniques zur Steuerung von 22 Kühlturmlüfter in zwei Kühltürmen eingesetzt. Das Kraftwerk liegt am Potomac Fluss, etwa 50 km südlich von Washington, USA. Die neuen Antriebe ersetzen ein System, das erstmals 1975 installiert wurde, und bieten zahlreiche Vorteile. Die Lüfterdrehzahl kann nun variiert werden, um dadurch den Stromverbrauch bei niedriger Last zu verringern; der Windmühleneffekt (Rotation bei deaktiviertem Lüfter) aufgrund eines fehlenden Bremssystems erübrigt sich; die Gefahr des Einfrierens im Winter minimiert sich; Vibrationen werden gemindert, ohne den Lüfter abschalten zu müssen und die saisonale Lüfterblattverstellung, die erforderlich war, um eine Überlast des Motors im Winter sowie eine niedrigere Luftzufuhr im Sommer zu verhindern, erübrigt sich auch. Allein der Arbeitsaufwand für die Lüfterblattverstellung führte zu erheblichen Kosten. Die Betreiber sparen nun an die 38.000 US-$ pro Jahr ein.
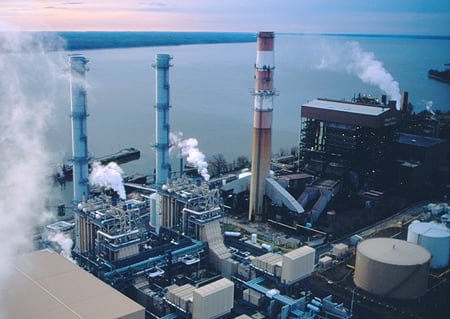
Energie- und Kostenreduzierung, ohne die Effizienz des Kühlturms zu beeinträchtigen
• Um bisher den Energieverbrauch und die Kühlkapazität zu regulieren, mussten die 200 PS starken netzbetriebenen Ventilatormotoren einzeln zugeschaltet werden, da sie stets mit voller Drehzahl liefen. Mit dem neuen Antriebssystem kann nun die jeweilige Lüfterdrehzahl und damit die Kühlung für unterschiedliche Lasten variiert werden. Alle Lüfter bleiben nun in Betrieb für eine beste Kühlturmeffizienz mit einem wesentlich geringeren Energiebedarf. Das Kühlsystem bewegt nur soviel Luft wie es erforderlich ist, um Wärme zu entziehen, was einen geringeren Energieverbrauch zur Folge hat.
• Vibrationen bei einzelnen Lüftern unter Kontrolle halten, die bisher abgeschaltet werden mussten – selbst wenn die Last- und Kühlanforderungen hoch sind. Durch die neue Antriebstechnik bietet sich nun die Möglichkeit, alle Lüfter in Betrieb zu halten, wobei einige mit geringerer Drehzahl betrieben werden können, um Vibrationen zu vermeiden. Dies sorgt für eine optimale Kühlung je nach Bedarf und Blocknutzung.
• Ein weiterer Aspekt war die saisonal erforderliche und manuell durchgeführte Anpassung der Lüfterblattabstände, die aufgrund der unterschiedlichen Luftdichte im Sommer und Winter notwendig war. Dies erforderte bis zu 480 Mannstunden pro Jahr, was einen erheblichen Wartungsaufwand verursachte, einschließlich weiterer Anforderungen wie Kranmiete und Sicherheitsmaßnahmen.
Anlagen-Management und Schutz
• Die Lüfter verfügen über eine 4,88 m (16 ft) lange Glasfaser-/Metallwelle, die das Lüftergetriebe mit dem Motor verbindet. Ohne Bremsanlage war der Windmühleneffekt bei Lüftern im Leerlauf ein ständiges Problem, das manchmal zu schlechten Startszenarien führte, die eine Überlastung des Motors, hohe Drehkräfte auf die Antriebswelle und sogar zu Getriebeproblemen führte. Der Einsatz des Frequenzumrichters Unidrive M700 ermöglicht nun einen Sanftanlauf der Ventilatoren. Damit minimieren sich beim Einschalten des Lüfters die Drehmomentspitzen auf die Welle und der Windmühleneffekt erübrigt sich. Die Motoren werden nicht länger den hohen Strömen ausgesetzt, wie sie bei einem Direktstart auftreten.
• Eisbildung und Auftauen ist ein Problem in Kühltürmen. Das bestehende System erforderte eine Drehzahlumkehr des Lüfter, sobald sich Eis an den Seitenwänden des Kühlturms bildete. Dadurch sollte das Eis an den Einlässen der Kühltürme aufgetaut und die mechanische Belastung reduziert werden. Denn diese kann zu Schäden am Kühlturm bis hin zu dessen Einsturz führen. Die Möglichkeit der variablen Lüfterdrehzahl sorgt nun für einen ordnungsgemäßen Luftstrom auch bei kalter Witterung und die Unterkühlung und somit die Bildung von Eis wird verhindert. Selbst bei widrigsten Wetterbedingungen müssen die Lüfter nun nicht länger in entgegengesetzter Richtung betrieben werden.
„Wir haben uns für drehzahlvariable Antriebe entschieden und dafür zunächst drei Hersteller in Betracht gezogen“, erklärte Mark Leigh, technischer Berater des Kraftwerks. „Control Techniques war jedoch der einzige Anbieter, der die sehr kurzen Projektlaufzeiten, die wir vorgegeben hatten, einhalten konnte . Sie waren zudem technisch äußerst kompetent und schlugen eine für uns optimale Lösung vor.“
Die Frequenzumrichter Unidrive M700 von Control Techniques mit Echtzeit-Ethernet-Funktion wurden im Kontrollraum des Kraftwerkes installiert, wo sie nun die Steuerung der 22 Kühlturmlüfter übernehmen. Die Umrichter sorgen für eine hohe Leistungsfähigkeit und eine flexible Steuerung sowohl von Standardasynchron- als auch von Permanentmagnetmotoren. Am wichtigsten ist jedoch, dass der neue Unidrive M700 mehr Steuerungsfunktionen für den gesamten Prozess bietet und die bisher notwendige saisonbedingte Verstellung der Ventilatorblätter nunmehr entfällt.
„Bei einem netzbetriebenen Ventilatormotor sind die Variablen der Lüfterblattabstand und die Luftdichte verbunden mit einer festen maximalen Motorleistung und einer definierten Drehzahl, die in diesem Fall 1750 U/min betrug“, so Leigh. „Im Gegensatz dazu sind die Variablen bei einem drehzahlveränderbaren Lüftermotorantrieb die Drehzahl und die Luftdichte bei einer maximalen Leistung und einem festen Lüfterblattabstand. Der Arbeitsaufwand für die Drehzahlanpassung mittels Einstellung des Blattabstands entfällt, da diese nun über den Frequenzumrichter erfolgt. Wir schätzen, dass die Einsparung in etwa vier Arbeiter für drei Wochen bzw. 480 Mannstunden umfasst, mit jährlichen Kosten von etwa 38.000 US-$.“
Fordern Sie weitere Informationen an…