AUTOMOBILBRANCHE
Viele Automobilhersteller zeigen ernsthaftes Interesse an der additiven Massenherstellung von Metallteilen. Sie alle führen Tests durch, richten Pilotproduktionseinheiten ein und verfeinern ihre Strategie.
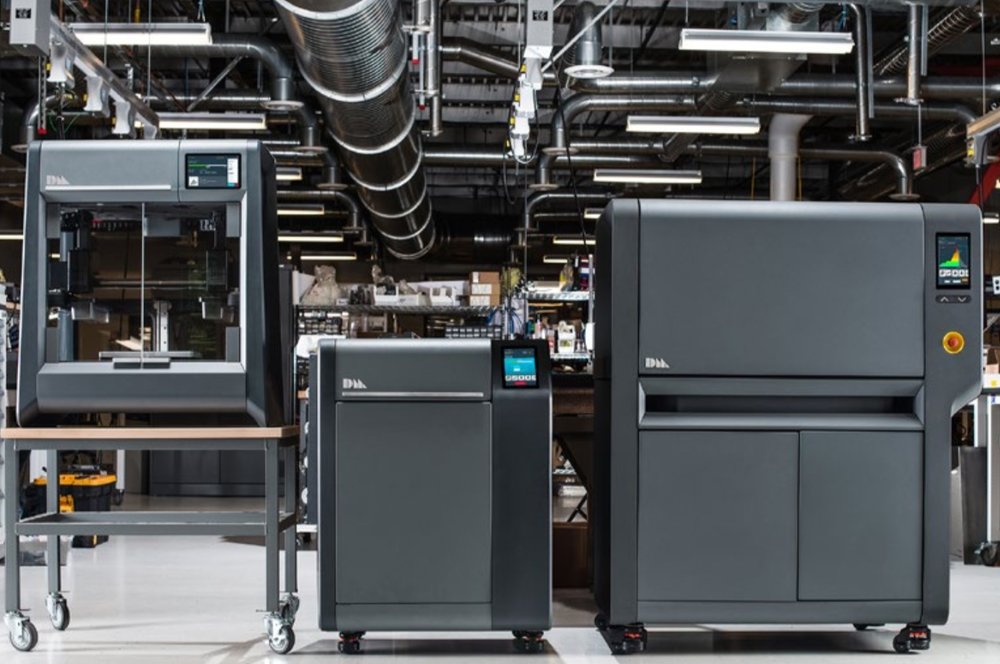
Auf dem Papier erscheint es bereits sicher, dass additive Fertigungsverfahren in den kommenden Jahren florieren werden. So können mit einer einfachen
CAD-Datei ohne Werkzeuge und Bearbeitungsabfolgen Metallteile hergestellt werden. Diese Aussicht würde sicher die Aufmerksamkeit von Automobilherstellern wecken. Allerdings ist von der Theorie und den Tests in einer F&E-Umgebung bis hin zu der tatsächlichen Bereitstellung im industriellen Umfeld immer ein weiterer Schritt notwendig. Außerdem zeigen Prozesse, die unter überwachten Bedingungen eines Labors demonstriert wurden, nicht unbedingt immer dieselbe Leistung oder können möglicherweise in einer Produktionsumgebung nicht im gleichen Maßstab reproduziert werden. Selbst Automobilhersteller können nicht das Risiko eingehen, diese Technologie zu ignorieren. Sie können aber ebenso wenig ihre traditionellen Produktionsverfahren wie Fräsen und Schmieden aufgeben, die sich über mehrere Jahrzehnte bewährt haben, und diese durch Technologien ersetzen, die längst noch nicht ausgereift sind – ganz gleich, wie vielversprechend diese erscheinen mögen. Obwohl diese neuen Verfahren die erforderlichen Ziele hinsichtlich Qualität und mechanischer Stabilität zu erfüllen scheinen, sind sie nicht profitabel genug, wenn große Mengen an Metallkomponenten gefertigt werden. Dennoch scheinen sie eine bessere Wiederholbarkeit zu liefern, was von Vorteil ist, wenn an verschiedenen Standorten identische Teile produziert werden müssen.
Die meisten Automobilhersteller haben bereits Tests an Prototypen mit angeblich verheißungsvollen Ergebnissen durchgeführt. Manchen von ihnen haben sogar damit begonnen, eine sehr kleine Serie an Teilen für Rennwagen oder auch Komponenten zu produzieren, die eine hochgradige Anpassung erfordern. Wieder andere wie Daimler denken nun ernsthaft über die Produktion von Ersatzteilen nach. Es gibt nur einige wenige Hersteller wie BMW und Daimler, die auf die Industrialisierung dieser Verfahren für die Massenproduktion von Teilen für Serienfahrzeuge in naher Zukunft setzen.
Die Einschränkungen der additiven Fertigung
Die größten Einschränkungen bei der additiven Fertigung bestehen in der geringen Produktivität und den Beschränkungen bei der Größe der gefertigten Metallteile. 3-D-Drucke sind derzeit nur bei kleinen Teilen mit komplexen Formen, einem Durchmesser von
maximal 100 mm und einem Gewicht von höchstens 400 g möglich. Bei der Laserfusion können jedoch Teile mit einer Länge von 600 bis 700 mm bearbeitet werden. Die mechanische Struktur der gefertigten Teile ist vollkommen zufriedenstellend. Allerdings kann man nach wie vor nicht erwarten, dass die Maschinen gebrauchsfertige Teile ausgeben. Es sind diverse Sinter-, Endbearbeitungs- und Oberflächenbearbeitungsverfahren notwendig. Die additive Fertigung geht also noch immer mit einer geringen Produktivität einher und wird erheblich von den zusätzlichen Endbearbeitungsschritten beeinträchtigt.
Alle diese Faktoren veranlassen die Automobilhersteller dazu, sich nicht vorschnell für diese Technologie zu entscheiden. Auch die Macht der Gewohnheit und das Vertrauen auf traditionelle Herstellungsverfahren hindert sie an der Umstellung. Dennoch scheint keiner der Automobilhersteller der Zukunft den Rücken kehren zu wollen. Alle von ihnen untersuchen sowohl das Potenzial als auch die durch additive Fertigung erzielten Fortschritte genau. Zweifelsohne stellt sie eine attraktive Alternative für die Herstellung komplexer Teile dar. Da sie kostspieliger ist als herkömmliche Verfahren, wurden alle Möglichkeiten zur Kostensenkung so weit wie möglich ausgeschöpft, indem die Funktionen des Teils erhöht wurden. Außerdem muss den Entwickler bewusst sein, dass sie Formen wie Gitterstrukturen und interne Kanäle mit komplexen Formen generieren können, die andernfalls nicht möglich wären. Deshalb zieht die additive Fertigung ein starkes Interesse von Automobilherstellern von Komponenten auf sich, die zur Flüssigkeitsentleerung und Filterung verwendet werden.
Ein weiterer Vorteil der additiven Fertigung besteht darin, dass nur die exakte Materialmenge verwendet wird, die zur Herstellung des Teils benötigt wird. Dadurch fällt weniger Gewicht an. Besonders für Hersteller von Motorkomponenten ist dies ein wichtiger Vorteil, da das Gewicht sich auf den Benzinverbrauch des Fahrzeugs auswirkt. Bei manchen Teilen kann das Potenzial zur Verringerung des Gewichts bis zu 50 % betragen, was bei Elektrofahrzeugen eine wichtige Rolle spielt, da die angestrebte Reichweite teilweise von der Fahrzeugmasse abhängt.
Trotzdem: „Bei Produktionsmengen von 70.000 bis 100.000 Einheiten bleiben die Kosten dennoch viel höher und die angestrebte Gewichtsreduktion ist als Argument nicht überzeugend genug“, so Fabian Krauß, Leiter der Geschäftsentwicklung im Automobilbereich bei EOS. „Flugzeughersteller sind bereit, 15.000 € zu investieren, um das Gewicht um 1 kg zu verringern, Automobilhersteller dagegen würden nur 15 € dafür ausgeben.“ Das bedeutet, dass die additive Fertigung beispielsweise durch zusätzliche Funktionen am Teil oder durch die Reduzierung von Montagekosten mehrere Maßnahmen zur Kosteneinsparung ergreifen muss, um Spitzenreiter zu werden.
Der 3-D-Metalldruck
Die Umstellung auf die additive Fertigung bei der Massenherstellung von Teilen im großen Maßstab ist noch weit davon entfernt, Wirklichkeit zu werden. Im Bereich der Produktivität und Profitabilität müssen noch Fortschritte
erzielt werden. Durch ein neues 3-D-Metalldruckverfahren scheint ein erster Schritt unternommen worden zu sein. Bei diesem Herstellungsprozess wird eine Bindeschicht mit Pulver aufgetragen, mit der ein so genannter Grünling produziert werden kann, der anschließend ein Loslösungs- oder Sinterverfahren durchlaufen muss. Dies ermöglicht im Vergleich zu traditionellen Laserschmelztechniken schnellere Durchsatzraten.
Der amerikanische Hersteller Desktop Metal beispielsweise verkündete, dass er 2018 ein 3-D-Metalldrucksystem zur Massenproduktion von Teilen mit einer Größe von 330 mm x 330 mm x 330 mm einführen wird. Die Maschine erreicht Produktionsraten von bis zu 8200 cm3/h, was laut des Herstellers hundertmal schneller als laserbasierte Verfahren ist. Seinen Angaben zufolge führen die Verwendung eines kostengünstigeren Pulvers, ein höherer Durchsatz und eine vereinfachte Nachbearbeitung zu Stückkosten, die mit traditionellen Herstellungsverfahren mithalten können und bis zu zwanzigmal niedriger sind als aktuelle 3-D-Metalldrucksysteme.
Lasersysteme bieten jedoch den Vorteil, dass sie ein größeres Erstellungsvolumen haben. Das von GE Additive 2017 angekündigte System „Atlas“ bietet beispielsweise einen Bauraum von 1.100 x 1.100 x 300 mm.
Verschiedene industrielle Strategien
Die BMW Gruppe gehört inzwischen zu den strategischen Partnern von Desktop Metal, welche die Übernahme des Verfahrens in der Automobilbranche vorantreiben sollen. „Nachdem wir das Potenzial der Technologie erkannt
hatten, gehörten wir zu den Ersten, die in das Unternehmen investierten,“ so Uwe Higgen, stellvertretender Direktor von BMW i Ventures. Jens Ertel, Leider des Additive Manufacturing Centre der deutschen Unternehmensgruppe fügte hinzu: „Für uns war es offensichtlich, dass die additive Fertigung für mehr als nur die einfache Prototypenentwicklung benutzt werden konnte. Wir erforschen unterschiedliche Materialien und Technologien. Wir versuchen herauszufinden, für welche Projekte und Teile die additive Fertigung profitabel ist und wo sie unsere Standards erfüllt. Wenn wir bei den Maschinen und Materialien Fortschritte beobachten, können wir absehen, wie sich die Zukunft gestalten wird. Mit Desktop Metal planen wir nicht nur eine Prototypenentwicklung in Hochgeschwindigkeit, sondern auch die Massenproduktion von Automobilteilen.
Auch der Leiter von Additive Manufacturing Metal bei BMW blickt dem Ganzen zuversichtlich entgegen: „Die Zukunft des 3-D-Drucks ist offensichtlich die Massenproduktion. Künftige Maschinengenerationen werden in der Lage sein, eine viel größere Anzahl an Komponenten in einer kürzeren Zeit zu produzieren. Das bedeutet, dass wir die Wirtschaftlichkeit und die Präzision sowie den Nutzen des Potenzials eines geringeren Gewichts und einer werkzeuglosen Herstellung steigern können.
Ebenso wie BMW gehört auch Daimler zu den Herstellern, die demonstrieren, dass sie an die additive Fertigung glauben. Der Automobilhersteller, eine Niederlassung von Airbus Premium Aerotec und der 3-D-Drucker-Hersteller EOS haben 2017 verkündet, dass sie mit dem 3-D-Metalldruck in die Produktionsphase gehen werden. Das Ziel Ihres Projekts „NextGenAM“ besteht darin, ein automatisiertes Herstellungssystem für die Massenproduktion zu entwickeln. Um die Kosten zu senken und zu ermöglichen, dass es schneller in der Produktion zum Einsatz kommt, versuchen sie, die Gesamtproduktionszeit, einschließlich der Verfahren vor und nach dem Druck, zu verringern, zumal diese in der Regel manuell erfolgen und 70 % der Gesamtkosten in der additiven Fertigung ausmachen. So kann der Nachteil der geringen Geschwindigkeit bei der additiven Fertigung durch die Optimierung, Automatisierung und einen flüssigeren Ablauf des Produktionsprozesses ausgeglichen werden.
Produktion von Ersatzteilen und Werkzeugen
Es müssen neue Herstellungsarten gefunden werden, die sich für die spezifischen Bedingungen der additiven Fertigung eignen. Die drei Hersteller haben mehrere Millionen Euro in dieses Projekt investiert, das zum Bau eines Zentrums zur automatisierten additiven Fertigung, dem Technologiezentrum von Premium Aerotec in der deutschen Stadt Varel führte. Daimler wird dort auch sein Fachwissen bei der Herstellung von leichtgewichtigen Flugzeugteilen einfließen lassen. Diese Teile werden mittels eines Laserdrucksystems in einem Medium verwendet, das sie extrahiert und dann automatisch mit einem führerlosen Fahrzeug (AGV ) an die
Bearbeitungsstationen zur Endbearbeitung, Temperierung usw. weitertransportiert.
Durch die Abschaffung manueller Eingriffe und die Verringerung von Verzögerungen zwischen den einzelnen Schritten kann jetzt möglicherweise die geringere Produktivität des additiven Fertigungsprozesses ausgeglichen werden. Der erste Teil, der in geringer Menge hergestellt wird, ist ein Fahrzeugteil von Mercedes-AMG, bei dem ein geringeres Gewicht ausschlaggebend ist.
Die BMW Group ist eines der ersten international tätigen Unternehmen, bei dem ein Metall-3D-Drucksystem des Typs Studio System zum Einsatz kommen wird.
Die Abteilung Additive Fertigung der BMW Group arbeitet eng mit dem 3D-Drucker-Hersteller Desktop Metal zusammen, um möglichst schnell eine gute Marktdurchdringung zu erreichen. „Im Prototypenbau der Automobilindustrie ist das Metall-3D- Druckverfahren schon weit verbreitet. Derzeit arbeiten wir daran, Verfahren der Additiven Fertigung auch in anderen Bereichen zu nutzen, wie zum Beispiel der Entwicklung oder der kostengünstigen Massenproduktion. Allerdings ist das eine sehr anspruchsvoll Aufgabe. Denn die Einführung des 3D-Drucks wird nur dann von Erfolg gekrönt sein, wenn sich damit eine hervorragende Materialgüte, eine hohe Prozesssicherheit, ein durchdachtes Design und überzeugende Leistungen zu geringen Stückkosten erreichen lassen. Gemeinsam mit Desktop Metal wollen wir alle bisherigen additiven Fertigungsverfahren genau unter die Lupe nehmen. Uns geht es einerseits darum festzustellen, wie sich mit dem Studio System der Prototypenbau verbessern lässt. Andererseits möchten wir herausfinden, inwieweit sich das Production System auch für die Hochgeschwindigkeitsfertigung von Prototypen sowie die Massenfertigung von Automobilteilen der BMW Group eignet“, erklärt Jens Ertel, Leiter des Additive Manufacturing Center der BMW Group in München.
Daimler zählt auch bei der Produktion von Ersatzteilen auf die additive Fertigung. „Unser Ziel besteht darin, unseren Fertigungsprozess für Ersatzteile mithilfe des 3-D-Drucks komplett umzugestalten, “ so Ralf Anderhofstadt, Leiter des Projekts „CSP 3D Printing“ bei Daimler Buses. Langfristig geht es darum, Teile in Fällen leichter verfügbar zu machen, wo es bisher unmöglich war, schnell zu reagieren, und Kosten zu reduzieren sowie Abgabetermine zu verkürzen. Damit sichern wir uns einen Wettbewerbsvorteil. Wir haben mehr als 300 Plastikteile sowie 100 Metallteile gefunden, die sich gut dafür eignen. Die Produktion begann im Sommer 2017.“
Volkswagen scheint im Bereich der additiven Fertigung besonnener zu handeln als seine Konkurrenten. Ingo Hartmann, der Koordinator der additiven Fertigung innerhalb der Gruppe gibt an, dass der 3-D-Metalldruck trotz seiner Vorteile aufgrund seiner Kosten und relativen Langsamkeit sowie seiner Formgenauigkeit noch immer auf bestimmte Anwendungsbereiche begrenzt ist, und die Endbearbeitungsqualität noch optimiert werden muss. Seinen Aussagen zufolge ist der 3-D-Druck derzeit nur bei Produktionsserien von bis zu 200 Einheiten wirtschaftlich. Durch die Prozessoptimierungen sollte es bei Serien von 3.000 Teilen profitabel werden.
Durch seine Niederlassung Audi ist Volkswagen im Rennen. Alois Brandt, dem Leiter des Technology Development Innovation Managements zufolge hat die Gruppe verschiedene Möglichkeiten zum Druck von Metallfahrzeugteilen in geringen Mengen eruiert. Seiner Ansicht nach ist noch viel zu tun, bevor die Technologie eine hohe Durchdruckrate leisten kann. „Beim Audi A4 müssten wir beispielsweise mehr als 1000 Drucker installieren und sie bei maximaler Geschwindigkeit laufen lassen, nur um letztendlich Fertigungsteile zu erhalten, die teurer kommen als beim aktuellen Verfahren.“
Audi ist der Ansicht, dass 3-D-Drucke sich hauptsächlich bei der Werkzeugherstellung und kleinen Produktionsserien lohnen. Momentan ist die 3-D-Herstellung noch langsam und kostspielig und auch hinsichtlich der Größe der gefertigten Teile beschränkt. Der größte der drei Drucker im 3-D-Metalldruckzentrum von Audi kann bis zu 400 mm lange Teile bauen. Die Herstellung eines Metallrohrs mit einem Gewicht von 1 kg dauert einen ganzen Tag. Zusätzlich wird Zeit benötigt, um die Maschine zu programmieren und vorzubereiten und die nachfolgenden Endbearbeitungsschritte durchzuführen.
Der Schwerpunkt im 3-D-Druckzentrum liegt daher auf der Produktion von Stahl- und Aluminiumwerkzeugen mit Metallpulver und Laserschmelzen. Trotzdem geht Audi davon aus, dass diese Technologie in den kommenden Jahren schnell ausreifen wird und sie für die Herstellung von Teilen für Fahrzeugmodelle mit limitierter Serie attraktiv werden wird. Während das Unternehmen auf den technologischen Durchbruch wartet, baut es sein Know- how im Bereich des Aluminiumdrucks aus. Es wurden mehrere Autoteile wie Komponenten mit poröser Struktur gefertigt, die Fluidbehälter und die ersten Aufhängeteile beinhalten.
Nach einem Interview mit Christophe GROSJEAN vom CETIM
Produktivität: 3-D-Metalldrucke übertreffen die Leistung von Laserschmelzen
Die additive Fertigung umfasst eine Reihe von Technologien, die aufgrund einer CAD-Datei ein dreidimensionales Objekt durch die schrittweise Hinzufügung von Material bauen. Im Gegensatz dazu wird bei anderen Bearbeitungstechniken Material entfernt. Es gibt für alle Arten von Material wie Metalle, Keramik, Polymer usw. Verfahren.
„Bei Metallen wird eine thermische Nachbehandlung zur Reduzierung der Eigenspannung benötigt. Bei der Herstellung von Metallteilen mit additiven Fertigungstechniken sind stets Endbearbeitungsvorgänge, die Entfernung des Trägers, Ausschneiden, Spannungsabbau usw. erforderlich. Insbesondere kann die thermische Nachbearbeitung zur Verbesserung der mechanischen Eigenschaften des Teils verwendet werden,“ erklärt das Unternehmen CETIM, das seit mehr als 15 Jahren an der additiven Fertigung und deren technologischem Transfers arbeitet.
Der 3-D-Metalldruck unterscheidet sich ziemlich stark von der additiven Fertigung mit Laserschmelzen. Er wird in zwei Phasen ausgeführt. In der ersten Phase wird das Teil durch das Aufbringen von Schichten aus gebundenem Pulver geformt. Letzteres wird durch ein organisches Bindemittel zusammengehalten und von einem Multi-Jet-Druckkopf extrudiert. Die zweite Phase wird benötigt, um ein Teil mit der gewünschten Widerstandskraft zu erhalten. Nachdem das Bindemittel durch Verbrennung (Entbindern) entfernt wird, wird der so genannte„Grünling“ hart und in einem Sinterofen verdichtet, um das Bindemittel herauszubrennen, die Metallpartikel miteinander zu verschmelzen und so eine funktionelle Metallkomponente zu formen.
Diese Methode bietet im Vergleich zum Laserschmelzen mehrere Vorteile. „Während beim Laserschmelzen die Teile nicht übereinander positioniert werden können, erfolgen 3-D-Metalldrucke in einer Baukammer, in der die Teile gestapelt werden können. Somit kann eine größere Menge im selben Produktionslos gefertigt werden“, gibt CETIM zu bedenken. Neben der schnelleren Baugeschwindigkeit wird auch die Produktivität erheblich gesteigert. Ein weiterer Vorteil: Durch 3-D-Metalldrucke können Teile gedruckt werden, ohne dass dafür während der Bauphase ungeachtet der Oberflächenkanten spezielle Träger benötigt werden. Dies bietet wesentliche Vorteile bei der Endbearbeitungsphase, da sich die Kosten für die Bearbeitung der Teile in Grenzen halten, sowie bei der Entwicklungs- und Implementierungsphase.
Insgesamt werden laut CETIM durch Metalldrucke die Produktivität optimiert und die Kosten im Vergleich zum Laserschmelzen gesenkt. Und das Ganze, obwohl der Sintervorgang notwendig ist, weil Laserschmelzen mehr Schritte während der Endbearbeitung erfordert. Um zusätzlich die Baugeschwindigkeit beim 3-D-Druck zu beschleunigen, muss auch die Anzahl der Druckköpfe erhöht werden. Mehr Laserquellen wären schwieriger zu implementieren und würden zu erheblich höheren Kosten führen. Aus diesen Gründen liefern 3-D-Drucke ein großes Potenzial für die Entwicklung und Herstellung von kleinen Teilen mit komplexen Formen.
Der Centre Technique des Industries Méchaniques (CETIM) wurde 1965 auf Anfrage der Maschinenbaubranche gegründet, um Unternehmen Methoden und Fähigkeiten an die Hand zu geben, um die Wettbewerbsfähigkeit zu steigern, an der Standardisierung teilzunehmen, als Bindeglied zwischen wissenschaftlicher Forschung und Industrie zu agieren, den technischen Fortschritt zu fördern und an der Optimierung der Wirtschaftlichkeit und der Gewährleistung der Qualität mitzuwirken.
Das CETIM ist im Bereich der additiven Fertigung sehr aktiv und fördert und berät Hersteller beim kontinuierlichen Veränderungsprozess.
Fordern Sie weitere Informationen an…