www.konstruktion-industrie.com
26
'19
Written on Modified on
Bedienerfreundliches Be- und Entladesystem für Werkzeugmaschinen
Maschinenbeschickung einfacher und produktiver denn je.
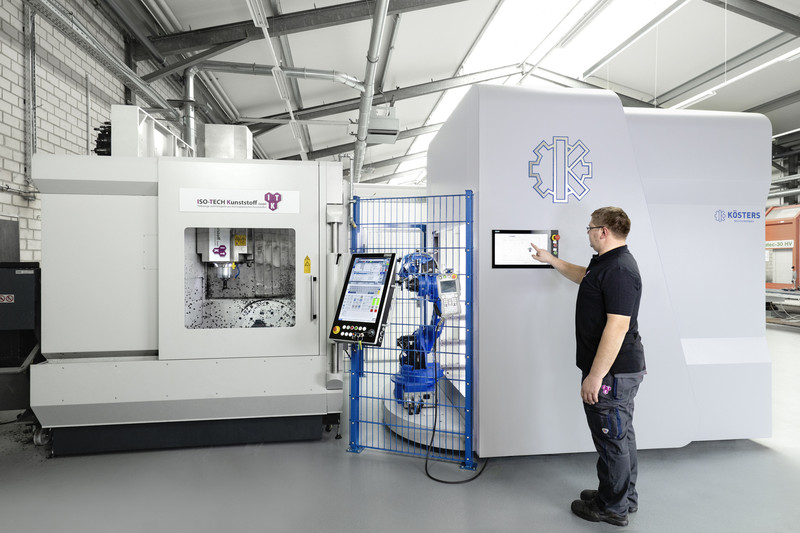
In der automatischen Beschickung liegt ein enormes Einsparpotenzial, das weiß man in Konzernzentralen ebenso wie in der Geschäftsführung von klein- und mittelständischen Unternehmen. Die Reduzierung von Nebenzeiten, die Steigerung von Flexibilität und Autonomie bis hin zu mannlosen Schichten – alles Fakten, die Begehrlichkeiten bei der Erschließung letzter Rationalisierungspotenziale wecken.
Dennoch sind Robotik-Sonderlösungen oftmals nicht gerade anwenderfreundlich, zudem teuer und wenig flexibel. Und: Sie können eine Komplexität in die Prozesse bringen, die der Anlagenverfügbarkeit wenig zuträglich ist und die Gesamtwirtschaftlichkeit im ungünstigen Fall sogar negativ beeinflusst. Genau aus diesem Grund hat sich Peter Kösters, Geschäftsführer Maschinenbau Kösters eine ganz spezielle Lösung ausgedacht.
Worauf es dem erfahrenen Maschinenbauer besonders ankam, bringt er so auf den Punkt: „Wir wollten eine vollautomatische Beschickungslösung mit Sechsachs-Roboter, die ohne jedwede Robotikkenntnisse zu bedienen sein sollte. Gleichzeitig sollte die Roboterzelle eine bis dato nie gekannte Flexibilität ermöglichen, die selbst die Bearbeitung von kleinsten Losgrößen erlaubt, was wiederum kürzeste Rüstzeiten voraussetzt.“
Um diese Vorgaben in die Praxis umzusetzen, stand eines von vorneherein fest: Der Anwender darf mit der Robotik nicht in Berührung kommen, das heißt, Teachen und Programmieren bleiben außen vor. Seine Aufgaben sollten sich auf einfachste Bedienschritte sowie auf die Bereitstellung von Rohteilen und den Abtransport der Fertigteile beschränken.
Pilotanwendung in der Kunststoffbearbeitung
Wie Kösters Maschinenbau diese Anforderungen in die Praxis umgesetzt hat, zeigt die erste Prototypenzelle, die bei dem renommierten Kunststoffspezialisten ISO-TECH Kunststoff in Ahaus im Einsatz ist. Das Unternehmen zählt zu den führenden Herstellern und Verarbeitern thermoplastischer Kunststoffe.
Das Produktportfolio besteht aus Halbzeugen und Fertigteilen, darunter Zahnräder, Rollen, Buchsen, Ringe, Hülsen und dergleichen mehr.
In der Fertigteil-Fertigung übernimmt die Roboterzelle die vollautomatische Beschickung eines Spinner Bearbeitungszentrums, auf dem diverse Kunststoffteile gefräst werden. Die Losgrößen reichen hier von einem Dutzend bis zu Kleinserien mit mehreren Tausend Einheiten, die Variantenanzahl geht gegen unendlich.
Was sofort ins Auge sticht, sind die stabile Ausführung und professionelle Gestaltung der Roboterzelle mit abgerundeten Kanten und einer überzeugenden Formensprache, die die Handschrift eines kundigen Industriedesigners verraten. Die Beladung der Anlage erfolgt besonders ergonomisch und einfach: Der Bediener legt die einzelnen Rohteile ungeordnet auf einer von drei Werkstückladen ab und schiebt diese voll bestückt in den Arbeitsbereich des Roboters.
Ab jetzt übernimmt ein YASKAWA Sechsachser des Typs MOTOMAN MH24 vollautomatisch die Be- und Entladung des Bearbeitungszentrums. Der Grund, warum dieser Roboter ohne Programmierung und ohne Teachen seitens des Anwenders auskommt, befindet sich an der Zellendecke: Hier ist ein hochleistungsfähiges 2D-Bildverarbeitungssystem montiert, das über die eigenentwickelte Prozesssteuerung mit dem YASKAWA-Roboter kommuniziert.
So erhält der Roboter die genauen Positionsdaten der Rohteile und kann die Teile selbsttätig der Reihe nach abgreifen.
Diese überzeugende Lösung war einer von mehreren entscheidenden Gründen für den Einsatz eines Sechsachsers von YASKAWA: „Für die reibungslose Kommunikation und Datenübermittlung zwischen Bildverarbeitung und Roboter mussten wir tief in die Steuerung des MH24 eingreifen.
Bei Robotern anderer Hersteller wäre dies entweder gar nicht oder nur sehr umständlich möglich gewesen. YASKAWA bietet hier mit der DX200 Steuerung alle Möglichkeiten, um uns die Arbeit enorm zu erleichtern“, so Kösters.
Aber zurück zum Arbeitsablauf: Mit einem gegriffenen Kunststoffteil fährt der MH24 durch die geöffnete Beladetüre des Bearbeitungszentrums zur Werkstückaufnahme. Hier entnimmt der Sechsachser mit seinem Fertigteilgreifer ein komplett bearbeitetes Teil, dreht das Greifsystem um 180 Grad und positioniert mit dem Rohteilgreifer ein unbearbeitetes Werkstück in der Aufnahme.
Anschließend legt der MH24 das Fertigteil ab und holt sich ein weiteres Rohteil aus der Werkstückschublade. Während dieses Bearbeitungskreislaufes kann der Anlagenbediener hauptzeitparallel die beiden anderen Schubladen der Beladezelle bestücken.
Umrüsten in Rekordzeit
Wie schnell die Anlage im Praxisbetrieb umzustellen ist, zeigt sich bei ISO-TECH immer dann, wenn ein Variantenwechsel ansteht. „Der Bediener muss lediglich die Abmessungen der neuen Teilevariante in das Graphikdisplay der Anlagensteuerung eingeben und die Greiferbacken des Roh- und Fertigteilgreifers mechanisch auf die entsprechenden Abmessungen einstellen.
Dank einer Schnellspannvorrichtung lässt sich diese Einstellung innerhalb weniger Minuten ausführen“, betont Kösters.
Diese beeindruckende Flexibilität, die sich mit einfachen Mittel realisieren lässt, erlaubt ISO-TECH die wirtschaftliche Bearbeitung von Losgrößen bis runter zu einem Dutzend oder noch weniger Teilen. Eine Umrüstzeit von unter zehn Minuten macht´s möglich.
Was sowohl ISO-TECH als Anwender wie auch Kösters als Hersteller der Roboter-Beladezelle freut, ist die hohe Verfügbarkeit der Prototypenzelle. Ausfälle gab es bislang keine, so dass auch eigentlich erwartete Nachbesserungen ausblieben. Dennoch wird es noch kleine Optimierungen geben, ehe diese Anlage als Standardzelle an den Start geht.
So soll der MOTOMAN MH24 bei künftigen Standardzellen durch den neueren MOTOMAN GP25 ersetzt werden. Für den Einsatz in den Roboterzellen sind alle YASKAWA-Roboter erste Wahl: „Auch der neue GP25 ist perfekt geeignet für Einsätze an Werkzeugmaschinen.
Dank seiner sehr schlanken Bauweise und der innerhalb des Arms geführten Medienleitungen kommt der Sechsachser auch mit beengten Platzverhältnissen bestens zurecht. Zudem ist das Handgelenk optimal gegen das Eindringen von Spänen geschützt. Und hohe Verfügbarkeit zählt ohnehin zu den YASKAWA Stärken“, so Kösters.
Mit der Pilotzelle, die ihre Bewährungsprobe bei Iso-Tech mit Bravour bestanden hat, eröffnet Kösters Maschinenbau ein neues Geschäftsfeld. „Wir sind überzeugt, mit dieser wegweisenden Standardzelle eine perfekte Beschickungslösung für Werkzeugmaschinen und Bearbeitungszentren bieten zu können.
Der große Vorteil unserer Zelle besteht in ihrer einzigartigen Flexibilität sowie in ihrer kinderleichten Bedienung, die keinerlei Robotikkenntnisse erfordert“, so Kösters.
www.yaskawa.de
Fordern Sie weitere Informationen an…