Hexagon ATS800 optimiert Inspektionen in der Luft- und Raumfahrt mit direktem Scannen und Automatisierung
Der ATS800 adressiert die Herausforderungen der Fertigung von sehr großen Teilen und ermöglicht eine automatisierungsfähige Inspektion.
hexagon.com
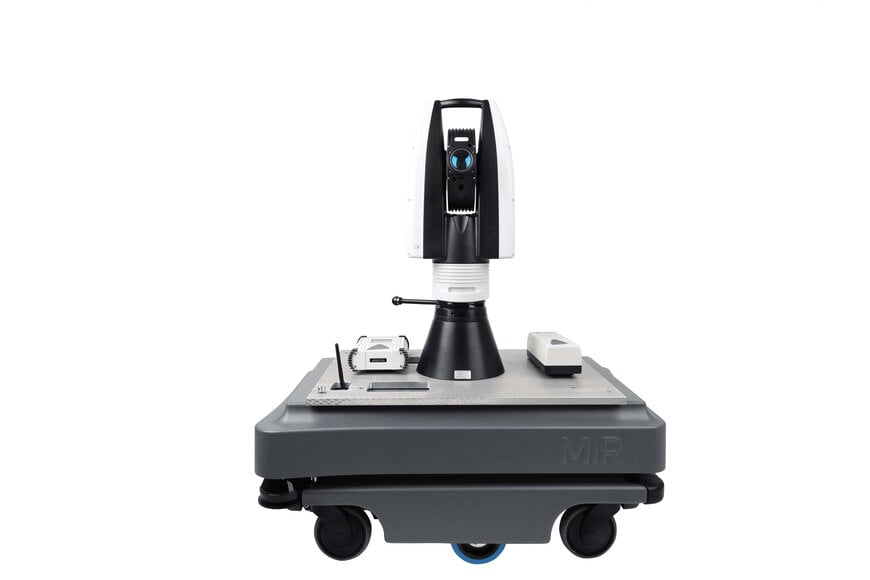
Während Luft- und Raumfahrtunternehmen sich trotz Fachkräftemangel und steigender Kosten ein Wettrennen in der Ausweitung ihrer Produktion liefern, präsentiert Hexagons Manufacturing Intelligence Division den Leica Absolute Tracker ATS800 – einen Lasertracker der nächsten Generation für komplexe Produktionsumgebungen mit hoher Variantenvielfalt und großformatigen Bauteilen. Das System stellt eine völlig neue Lösung für die Qualitätsprüfung in großformatigen Fertigungsbereichen in Branchen wie der Luft- und Raumfahrt oder Windenergie dar. Es bietet eine Direktabtastgenauigkeit, die vergleichbar mit der von Reflektor-Messsystemen ist, in einem tragbaren, leichten System.
FeatureDetect ist eine der Schlüsselinnovationen
Mithilfe nahtloser Integration in digitale und roboterbasierte Automationsprozesse reduziert der ATS800 Prüfzeiten, während er gleichzeitig Mess- und Prozessanpassungen in Echtzeit erlaubt. Eine seiner Schlüsselinnovationen ist FeatureDetect: Die automatische Merkmalserkennung identifiziert wichtige Bauteilgeometrien ohne manuelle Programmierung. Durch die daraus folgende Entlastung der Bedienenden ermöglicht FeatureDetect Produktivitätsgewinne sowohl bei automatisierten als auch manuellen Inspektionsprozessen. FeatureDetect arbeitet mit CAD-Daten oder unabhängig mit der integrierten hochauflösenden Panoramakamera des ATS800. Die Live-Bildübertragung im Breitbildformat erlaubt es dem System zudem, Eigenschaften direkt auf dem physischen Prüfteil zu erkennen, wodurch das Einrichten beschleunigt und die Prüfung optimiert wird.
Der ATS800 wurde für sicherheitskritische Industrien entwickelt, in denen die manuelle Prüfung von großen, komplexen Strukturen oft Engpässe verursacht. Deshalb kombiniert der Tracker hochpräzises, direktes Scannen und Reflektorverfolgung in einem kompakten System. Durch die auf wenige Minuten reduzierte Einrichtungszeit unterstützt es unbeaufsichtigte oder prozessbegleitende Inspektionen – von der Ausrichtung des Rumpfes bis hin zur Verlegung von Verbundwerkstoffen – ohne Abstriche bei Genauigkeit oder Rückverfolgbarkeit.
„Die Herstellerinnen und Hersteller stehen heute unter immensem Druck, ihre Produktion unter Einhaltung höchster Qualitätsstandards zu steigern. Dabei können traditionelle arbeitsintensive Verfahren nicht mithalten“, erklärt Rodrigo Alfaia, Laser Tracker Product Director bei Hexagon. „Der ATS800 minimiert den Zeitaufwand bei der Einrichtung und den Messaktivitäten vor Ort, ohne dabei Präzision einzubüßen. Wir automatisieren zudem die Inspektion von Großserien physisch und digital, indem wir datengetriebene Prozesse auf die operative Ebene bringen – sei es beim Scannen eines kompletten Flugzeugrumpfs über Nacht oder bei der Steuerung kritischer Montageprozesse in Echtzeit. Dafür sind keine komplexen Schulungen für das Bedienpersonal erforderlich.“
Digital automatisiertes, hochpräzises Scannen
Der ATS800 kombiniert Hexagons etablierte Laser-Tracking-Technologie mit einem hochleistungsfähigen Direktabtastverfahren in einem kompakten Gerät. Es führt hochpräzise, reflektorlose Messungen in Entfernungen von bis zu 40 Metern durch und erhebt detaillierte Daten zu wichtigen Merkmalen wie Kanten, Löchern, Schlitzen und Gewinden ohne physischen Kontakt oder Nahbereichsscannen. Für noch mehr Flexibilität sorgt die vollständige 3D-Reflektorverfolgung, die bei der Inspektion großer Strukturen und Baugruppen die Aus- und Einrichtung beschleunigt.
Die neue, KI-basierte FeatureDetect-Technologie entfernt zudem einen bedeutenden Engpass in der Messtechnik für große Strukturen, indem sie die zu messenden Merkmale und die dazu passende Methode identifiziert. Die Technologie kann über CAD oder eine Panoramakamera bedient werden, optimiert die Programmierung und ermöglicht flexiblere, autonomere Arbeitsabläufe, die weniger auf Expertinnen und Experten angewiesen sind.
Zudem ist das System mit gängigen Software-Plattformen wie PC-DMIS, SpatialAnalyzer und Alternativen von Drittanbietern kompatibel, sodass es sich unkompliziert in bereits existierende Inspektionsprozesse einfügt. Es ist automatisierbar und bietet Kundinnen und Kunden durch die HxGN Robotic Automation Software einen Plug-and-Play-Pfad zu skalierbaren Inspektionen mit hohem Durchsatz.
Roboter- und AGV/AMR-Automatisierung
Trotz seiner umfangreichen Funktionalitäten wurde der ATS800 mit Fokus auf Tragbarkeit und Flexibilität im Einsatz entwickelt: Seine kompakte Form erlaubt eine flexible Montage in jeder Ausrichtung – sogar kopfüber – und den nahtlosen Einsatz auf AMRs, Portalkranen, Aufzügen, Schienen und Roboterarmen. Dadurch ist ein sicherer und platzsparender Betrieb auch in stark frequentierten Fertigungsbereichen gewährleistet.
Dank des bewährten und umfassend unterstützten SDK lässt sich der ATS800 in komplexe Roboter-Workflows integrieren und ermöglicht so automatisierte Merkmalsmessungen, dynamische Teilverfolgung und eine geschlossene Prozessregelung in Echtzeit. Ob integriert in eine stationäre Lift-and-Rail-Kombination oder auf einem AMR zur Überwachung großer Baugruppen: Der ATS800 bietet Ingenieurinnen und Ingenieuren eine vielseitige Messtechniklösung für die Inspektion mit minimaler menschlicher Beteiligung oder eine kontinuierliche Qualitätssicherung.
So kommt der ATS800 bereits in der neusten PRESTO Qualitätsstation von Hexagon zum Einsatz: Hier wird das System mit Hochgeschwindigkeits-Robotik kombiniert, um die Qualitätsprüfung von Automobilkarossen zu automatisieren. Durch den Einsatz von reflektorloser Langstrecken-Scantechnik werden hier mehrere komplexe Merkmale mit nur einer einzigen Achsenbewegung auf einer vertikalen Hebebühne oder einer horizontalen Schiene geprüft. Das reduziert Zykluszeiten deutlich und erhöht die Wiederholgenauigkeit sowie den Durchsatz.
„Dritte Schicht“ Workflows und Echtzeit-Montage
Mit zunehmender Produktion in der Luft- und Raumfahrt sowie in anderen Branchen mit großen Strukturen wird die Möglichkeit, Übernacht- oder In-Prozess-Prüfungen durchzuführen, immer wichtiger. Mithilfe unbeaufsichtigter Scans, Echtzeit-Tracking und Ausrichtung der Unterbaugruppe ermöglicht der ATS800 Herstellerinnen und Hersteller Prozesse in der „third-shift“ vollständig digital rückverfolgbar durchzuführen. Ob bei der Führung der Rumpfintegration oder der schichtweisen Verbundwerkstoffprüfung, er gewährleistet hohe Präzision ohne Unterbrechung der Arbeitsabläufe.
Das Herzstück des Systems ist Hexagons TruePoint Interferometer, eine Messtechnologie der nächsten Generation, die Geräusche minimiert und selbst auf schwierigen Oberflächen oder bei sehr steilen Winkeln höchste Genauigkeit liefert. Wenn Bewegung notwendig ist, rastet Hexagons patentierte PowerLock-Technologie zur Wiedererfassung bewegter Reflektoren sofort wieder ein und gewährleistet so eine kontinuierliche Messung während der Montage in Echtzeit.
www.hexagon.com
Fordern Sie weitere Informationen an…